A comprehensive review of forward osmosis and niche applications
Received
1st March 2020
, Accepted 9th June 2020
First published on 10th June 2020
Abstract
Despite intense research effort over the past 15 years, industrial and commercial application of forward osmosis (FO) technology has been slow to become established. Here, the recent improvements in FO technology are critically reviewed, with barriers to full-scale application highlighted. A brief introduction to the FO process is given, with subsequent critical focus on advances in membrane fabrication techniques to minimize fouling and enhance forward flux (e.g. incorporation of fillers, nanostructured surfaces), hybrid processes incorporating combined benefit from concentration–dilution (e.g. fertilizer-based solutions for agricultural irrigation, coupling of gas field produced water–desalination brine processing), and tailoring and improvements in draw solutions (e.g., thermo-responsive polymers, hydrogels, nanoparticles etc.) for targeted applications with minimized reverse solute flux and draw solution regeneration cost. The pilot and full scale industrial applications and areas where FO shows distinct promise over mature technologies are summarized, with emphasis on companies operating in this space as well as the application of life cycle cost analysis to compare and contrast technology application for full economic costing of FO at the commercial scale. The scope for innovation and current impediments to FO technology adoption are comprehensively addressed.
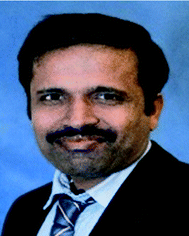 Lijo Francis | Dr Lijo Francis is currently working as a Scientist at Qatar Environment and Energy Research Institute (QEERI), Doha, Qatar. He received his PhD in Chemical Sciences and Technology from the University of Genova, Italy in 2010. Then he pursued his postdoctoral research at the National University of Singapore (NUS, Singapore) and at the King Abdullah University of Science and Technology (KAUST, Saudi Arabia). Dr Lijo Francis has received several renowned awards including Young Scientist Award (from Leed's University, UK in collaboration with Calicut University, India in 2009), Best Research Paper Award from European Desalination Society (EDS 2014, Cyprus), Young Academics Award from European Membrane Society (EMS 2015, Italy) and a couple of Seed Fund Awards for his outstanding research contributions to the Membrane Science and Renewable Energy Driven Water Reclamation Processes. Dr Francis is the author of 8 U.S/European patent applications/PCT and more than 80 international conference/journal research papers. |
 Oluwaseun Ogunbiyi | Oluwaseun Ogunbiyi is currently a research scientist at QEERI (Qatar Environment and Energy Research Institute), Hamad Bin Khalifa University (HBKU), a member of the Qatar Foundation. He completed his doctorate research in Chemical Engineering at the University of Nottingham in 2007. He has up to 13 years of core industrial experience as a senior process engineer at Wessex Water & GENECO and technical consultant at CH2M within the water and wastewater sector in the United Kingdom. He was actively involved as lead process consultant in the design, construction and operation of several sewage treatment works in the south west region of the UK. His research interests include membrane-based treatment technologies, domestic and industrial wastewater reuse applications and process improvement. He has publications related to his work in peer reviewed journals including Chem. Eng Research and Design and Journal of Membrane Science and Desalination. |
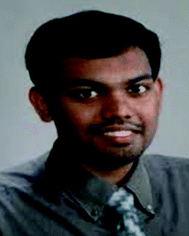 Jayaprakash Saththasivam | Dr Jayaprakash Saththasivam is working as a Scientist at Water Center, Qatar Environment and Energy Research Institute. He received his PhD degree in Mechanical Engineering from the National University of Singapore. His research interest are mainly in developing efficient treatment for wastewater and reuse. He has vast experience in designing heat and thermal systems and automated performance monitoring and control systems as well as building pilot plants related to wastewater treatment. |
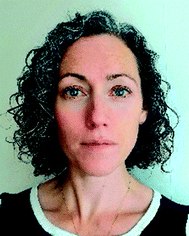 Jenny Lawler | Dr Jenny Lawler is the Senior Research Director of the Water Center at QEERI. She received her PhD in Membrane Separations from Dublin City University, Ireland. Her research focuses on the development of novel technologies and membrane-based strategies to solve environmental problems. She is particularly interested in the targeting of contaminants of emerging concern in the environment, especially those that have impact on human health. QEERI is at the forefront of development of technologies for protection of public health including treatment of water and other environmental matrices. |
 Zhaoyang Liu | Dr Zhaoyang Liu is Senior Scientist in Qatar Energy and Environment Research Institute (QEERI), Doha, Qatar. He received his PhD degree in Environmental Engineering from Dalian University of Technology, China. His research interests involve wastewater treatment and water desalination through process optimization and material development. He currently is engaging in multiple research projects as a lead for industrial and municipal wastewater treatment, with the subjects of oil/gas produced water treatment, purification of treated sewage effluent, and recycling of building grey water. He also holds 6 US and PCT patents related to water treatment. |
Water impact
This article critically reviews the recent improvements in FO technology, and highlights the niche applications where FO shows distinct promise over mature technologies in desalination, municipal/industrial wastewater treatment, fertilizer-based solutions for agricultural irrigation, etc.
|
1. Introduction
Water scarcity is a pressing global issue and has driven the rapid development and use of various technologies to tackle it. Membrane technology is one of the major technologies used for water desalination and wastewater treatment due to the high quality of its product water after membrane filtration. Forward osmosis (FO) is an evolving and promising membrane-based water treatment process, which has been studied intensively from both academia and industry perspectives in recent decades.1 When compared with pressure-driven membrane processes, the driving force in the FO process is the osmotic pressure gradient between both sides of a semipermeable membrane, which allows water to permeate from a low osmotic pressure region to the high osmotic pressure region without any external hydraulic pressure. Solutions with low and high osmotic pressure are known as feed solutions (FS) and draw solutions (DS), respectively. Water permeates from the FS to the DS through the FO membrane during the osmotic process until the osmotic pressure of the FS and DS reaches equilibrium. Thus the DS gets diluted and the FS gets concentrated during the process. It has been reported that some of the advantages of FO include lower membrane fouling propensity and greater energy efficiency compared to the reverse osmosis (RO) process.2–5 FO has been applied to various areas including desalination, wastewater treatment, food processing, district cooling and power generation amongst many others.6–9
Despite the high potential that the FO process has, it has not yet been fully commercialized due to several challenges, such as low membrane flux, concentration polarization, reverse solute flux, and high energy cost for the DS regeneration process.10 The successful implementation of the FO process in industrial applications relies heavily on improvements in multiple aspects, including membrane properties (water flux, concentration polarization and fouling mitigation), draw solutes (osmotic pressure, reverse solute flux and regeneration), and hybridization of the FO process with other processes.1,11 All of these aspects need to be improved collectively, and the improvement in one aspect might not necessarily be good enough for FO to become commercially competitive with other technologies.
In this review article, we extensively discuss the aspects of membrane properties, draw solute selection, fouling mitigation, and various niche applications of FO. This article highlights comprehensive information related to: (i) the development of different approaches for the fabrication of FO membranes; (ii) various draw solutions employed for FO process operation, i.e. draw solutions based on the categories of regeneration, direct use and disposal; (iii) an understanding of membrane fouling factors and their mitigation strategies; (iv) identification of niche applications of the FO process, which provide a comprehensive overview on the landscapes where FO could outperform other technologies. The niche applications include desalination, brine management, zero liquid discharge (ZLD), wastewater treatment and reuse, produced water treatment, food and dairy industry, chemicals and pharmaceuticals industry, electronics industry, district cooling and irrigation. Fig. 1 shows an illustration of the various components of the FO process. After the niche applications section, the article delves further into the recent commercialization approaches of the FO process at various locations. Finally, the article describes the life cycle cost analysis (LCCA) and techno-economic feasibility of FO and hybrid FO processes for different applications that have been investigated by various authors. This LCCA and the techno-economic feasibility study are very important exercises that are undertaken in order to advance this technology to the market.
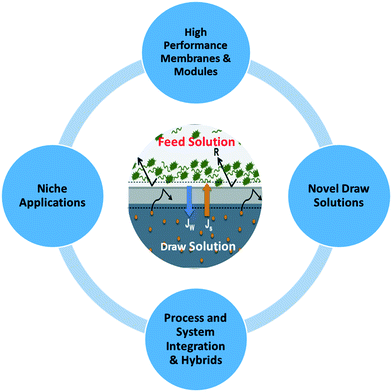 |
| Fig. 1 Different components of the forward osmosis system. | |
2. Forward osmosis membranes
Many industries including desalination and wastewater treatment are adopting membrane-based technologies due to their advantageous features, such as low energy consumption, small footprint, easy scale-up, etc. FO is a membrane-based low energy water separation process. An ideal FO membrane is characterized by a highly water permissible (A) active layer, which could minimize the reverse solute permeation (B), and a support layer which is capable of enhanced mass transfer and minimized concentration polarization effects.11,12 An efficient FO membrane must be mechanically stable, chemically resistant and less vulnerable to the fouling phenomenon. In water desalination FO processes, salt rejection is one of the important membrane criteria where an RO or nanofiltration (NF)-like active layer is required and explored in FO membranes to reject monovalent and multivalent ions or other large molecules, respectively.3,13 Several polymeric materials have been used to fabricate FO membranes. In the initial phase, some of the more commonly explored FO membrane materials include cellulose acetate (CA), cellulose triacetate (CTA), polyethersulfone (PES), and polybenzimidazole (PBI).14–23 At the later phase, FO membranes were fabricated using polyamide thin film composites (TFC) via interfacial polymerization (IP) on polysulfone-based substrates, sulfonated substrates, cellulose acetate propionate (CAP) substrates and non-woven electrospun nanofibrous substrates.18,24–27 The most common methods used for the fabrication of FO membranes are the non-solvent induced wet-phase inversion (NIPS) method formulated by Loeb and Sourirajan28 and thin-film composite (TFC) formation on porous substrates via interfacial polymerization introduced by Cadotte.29 In TFC membranes, thin-films are developed on the porous substrate by the in situ IP reaction between two monomers: namely, aqueous polyfunctional amines and apolar acid chloride solutions. TFC membranes show better FO process performance compared to conventional cellulose-based membranes. Other FO membrane fabrication methods are the layer-by-layer (LbL) coating of very thin layers of cations and anions on a charged porous support layer,30,31 and fabrication of biomimetic FO membranes by the incorporation of aquaporin.32,33 The most commonly used FO membrane materials and FO membrane fabrication methods are shown in Fig. 2. The state-of-the-art of the design and fabrication of TFC-FO membranes with their essential characteristics is depicted in Fig. 3.
 |
| Fig. 2 Commonly used materials and methods for the fabrication of FO membranes. | |
 |
| Fig. 3 State-of-the-art of the design of TFC-FO membranes. | |
Breton, in his dissertation entitled “water and ion flow through imperfect osmotic membranes” published in 1957, mentioned the theoretical hypothesis and experimental evidence of the semipermeable behavior of a cellulose acetate membrane in saline water.34 In 1963, Loeb and Sourirajan reported a phase inversion technique for the fabrication of osmotic membranes from a casting solution of cellulose acetate, acetone and aqueous magnesium perchlorate. The fabricated membrane was tested for the demineralization of seawater and it was found that the membrane was capable of producing a flux of 5 to 11 gallons of 0.05% NaCl water per sq. foot per day from a brine solution containing 5.25% NaCl, under a pressure of 1500 to 2000 psig.28 In 1976, Kessler and Moody reported the extraction of potable water from seawater using a concentrated solution of nutrients and a semipermeable membrane. They used CA membranes for fresh water reclamation from low quality water into a concentrated glucose–fructose solution, and compared the results with the predicted values.35
In 1965, Batchelder utilized a cellulose-based semipermeable membrane and dissolved volatile solutes such as sulfur dioxide in seawater or fresh water as the DS and seawater as the FS, in order to facilitate the FO process.36 Hydration Technology Innovation (HTI), established in 1986, commercialized the CTA FO membrane with a net or nonwoven support. The initial focus was on separating liquids and concentrating beverages and food products, with later development of flat sheet, spiral wound, and hollow fiber membrane elements for a wide range of water reclamation applications. HTI membrane water filtration systems were successfully employed by global military forces and humanitarian disaster relief organizations especially for the reclamation of fresh water from impaired quality storm waters.37
In 2005, McCutcheon et al. demonstrated a novel FO desalination process using an ammonium bicarbonate DS in order to collect fresh water from an impaired quality FS through a semipermeable polymeric FO membrane. A high osmotic gradient across the FO membrane was created by the highly soluble ammonium bicarbonate DS, which yielded high water fluxes. Ammonium bicarbonate decomposes into ammonia and carbon dioxide gases upon moderate heating which can be separated and recycled as draw solutes, leaving the fresh product water.38 The FO process followed by a second step for the regeneration of the draw solute is known as indirect forward osmosis.
Most of the aforementioned investigations on the FO process were performed using cellulose acetate-based RO membranes and cellulose triacetate-based FO membranes from HTI. However, the resultant water flux was much lower than theoretical or predicted values due to several reasons such as internal and external concentration polarization effects (ICP and ECP). The FO process performance is characterized by intrinsic parameters such as the A, B and S values of the membrane. All of these values are primarily dependent on the membrane structure and solute type. Cath and coworkers have developed a common methodology in order to compare the membrane performance from the literature.39,40 Recently, there has been a significant development of CA and CTA-based flat sheet FO or hollow fiber FO membranes.15,18,19,21,41–44
The membrane structural parameter (S) is a key factor in determining FO membrane and process performance. Although S is an intrinsic characteristic of a membrane, it has been used to decide the internal concentration polarization (ICP) phenomenon within the support layer of the FO membrane. The S value is constant for a specific system and varies with respect to the FS and DS concentrations. Recently, many researchers have investigated the FO process in order to optimize the S value. The S value can be determined by using the following equation:
where
A is the water permeability (L m
−2 h
−1 bar
−1),
B is the salt permeability (kg m
−2 h
−1),
D is the salt diffusion coefficient,
Jw is the water permeation flux (L m
−2 h
−1)), and π
ds and π
fs are the bulk osmotic pressures of the DS and FS, respectively.
Water permeability, A, is given by the equation;
where Δ
P is the transmembrane pressure.
where
Q is the volume of water permeate collected over a period of time Δ
t, and
A is the effective membrane area.
In order to enhance the FO process performance by tuning the membrane structural parameters, researchers have introduced much advancement via chemical/physical membrane modifications and employing novel membrane materials and draw solutions. Several research groups have reported the achievement of high water flux by using a specially engineered TFC-FO membrane.24,45–48 Many researchers are interested in hollow fiber FO membranes especially because of the fact that they can be used for high volume applications due to their high packing density and large surface area to volume ratio which results in small module footprint.49–59 Bui et al. and Song et al. have reported the fabrication of highly porous nanofiber supports for high performance TFC-FO membranes.26,60 Toyobo introduced a large-sized FO hollow fiber membrane prototype in Singapore International Water Week in 2014.61 According to Bui et al., the nanofiber support structure has high porosity and highly interconnected pore structure which cause the reduction of ICP in an FO process. It was demonstrated that the nanofiber-TFC membranes yielded 2- to 5-fold higher water permeation than the commercial HTI CTA membranes. Zhao et al. discussed a novel TFC-FO membrane fabrication approach with an intermediate layer of graphene oxide and multiwall carbon nanotubes, which offers a limited CP phenomenon with expected separation performance.62 Song et al. correlated water permeation with the structural parameter (S) of the membrane. As per their findings, the S values of the HTI-FO membrane, polyimide (PI) TFC-FO membrane and two different nanofiber TFC-FO membranes were calculated to be 620 ± 80, 450 ± 50, 106 ± 8 and 80 ± 6 μm, respectively. At the same time, the FO water flux values (in L m−2 h−1) while using those membranes were observed to be 6.5, 13.4, 33.9 and 37.8, respectively, and as such they concluded that the S value has a significant role in determining the FO water flux. The sponge-like structure of the support layer of the PI-TFC-FO membrane possibly blocks salt diffusion and results in a lower net transmembrane osmotic pressure difference, whereas salt diffusion is highly favorable in the support layer of electrospun nanofibrous TFC-FO membranes due to their interconnected pore structure, which results in a higher net osmotic pressure gradient and enhanced flux.
Tang and co-workers fabricated high flux FO membranes using an LbL structure of poly (allyl amine hydrochloride) (PAH) and poly(sodium 4-styrene-sulfonate) (PSS) on a porous poly acrylonitrile (PAN) substrate.30,31 They have reported a FO water permeation flux of ∼100 L m−2 h−1 with the active-layer-facing-DS side using 2 or 3 M magnesium chloride as the DS and fresh water as the FS. Thus, the LbL method is very promising for the production of high permeation FO membranes. Recently, researchers showed great interest in biomimetic aquaporin membranes used for desalination and reuse applications. Aquaporin is reported to be the protein responsible for transporting and purifying water in living cells, and to be super-efficient and selective.63–65 High water permeability and high salt retention are very important features of aquaporin proteins incorporated in the FO membranes.32,33 In 2018, Ren and McCutcheon evaluated a novel commercially available hollow fiber FO membrane made using aquaporin proteins and reported that the membrane was good enough for application-based research and benchmarking purposes, with improvements in speed and in energy efficiency.66 Recently, the modification of conventional membranes by blending them with nanostructured materials has been a new trend in the fabrication of efficient and fouling resistant membranes.67–70 Apart from HTI, Aquaporin, Porifera, Modern Water, Trevi, FTSH2O, Toyobo and Oasys are the different start-ups that have been introduced into the market or are under development in the arena of FO commercial membranes and systems. Aquaporin introduced biomimetic hollow fiber and spiral wound membrane configurations, Toyobo introduced very special hollow fiber FO membranes and all other mentioned suppliers have introduced a spiral wound FO membrane configuration that could be deployed in the FO system. Recent investigations are based on nanostructured and fouling resistant TFC-FO membranes with hollow fiber and spiral wound configurations. The niche applications using those systems will be discussed in a later section of this article.
3. Draw solutions for forward osmosis
Forward osmosis is an osmosis-driven membrane separation process, which relies on concentrated draw solutions to draw fresh water across a semi-permeable membrane from feed solutions. Unlike pressure-driven membrane separation processes, the product of an FO process is not pure water, but a diluted draw solution. Therefore, a second process is often needed to regenerate draw solutions and simultaneously produce pure water. But there are some exceptions where the second process of draw solution regeneration becomes unnecessary, when diluted draws solutions can be directly used, or discharged if the FO process is purely used to concentrate feed solutions rather than produce pure water, as shown in Fig. 4. Since the regeneration process of draw solutions is normally considered as a cost-intensive process, the selection of draw solutions critically affects the practical applications of the FO process. An ideal draw solution is expected to have the following merits: 1) high osmotic pressure; 2) low reverse solute flux; 3) high diffusion coefficient to reduce ICP; 4) low cost for draw solute materials; 5) low cost for the regeneration process; 6) low toxicity. However, there may be some contradictions between these merits. For instance, draw solutes of small size, such as NaCl, tend to have high osmotic pressure and reduced ICP, but their sizes also cause the issue of high reverse solute flux. From the perspective of practical applications, a comprehensive overview of various draw solutions that have been reported in the literature will be provided. The draw solutions will be summarized based on the categories of regeneration, direct use and disposal, as shown in Table 1.
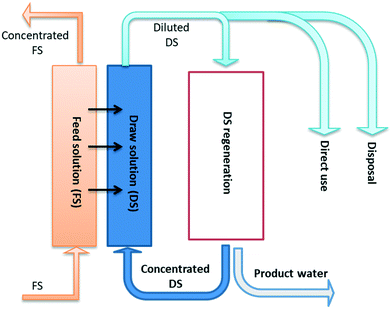 |
| Fig. 4 Schematic diagram of FO draw solutions with different handling approaches, including: regeneration, direct use and disposal. | |
Table 1 FO draw solutions based on the categories of regeneration, direct use and disposal
Categories |
Methods |
Draw solutes |
Advantages |
Disadvantages |
Regeneration |
Membrane |
RO/NF |
NaCl,71 Na2SO472 |
High osmotic pressure |
High reverse solute flux, high operation cost |
UF |
PAA-Na (ref. 73) |
Low reverse solute flux |
Low osmotic pressure |
Thermal |
Distillation |
NH3–CO2,74 acetone/tertiary amine,75 tri-methylamine76 |
High osmotic pressure, low cost |
Poor product water quality |
Hybrid |
MD |
PAA-Na (ref. 77) |
Low operation cost |
Low osmotic pressure |
Precipitation |
|
Al2(SO4)3,78 Al2(SO4)3-magnetic nanoparticles79 |
Low reverse solute flux |
Low osmotic pressure |
Stimulus response |
Magnetic |
Ferrite NPs +PEG80 |
Low operation cost |
Low osmotic pressure, high cost for draw solute materials |
Thermal |
PNIPAM+PVA/PSA81 |
Poly (ionic liquid)82 |
Direct use |
Dilution for drinks |
|
Sucrose, glucose, fructose83 |
No cost for solute regeneration |
Limitation in draw solute selection |
Dilution for fertigation |
|
Fertilizer (KH2PO4, Ca(NO3)2, NH4Cl)84 |
No cost for solute regeneration |
High reverse solute flux |
Disposal |
Dilution |
|
Oil/gas produced water, desalination brine water85 |
No cost for solute regeneration |
High membrane fouling |
3.1 Draw solutions with the need for regeneration
Draw solutions based on different regeneration methods were reviewed, including thermal separation, membrane separation (RO, NF, ultrafiltration (UF), thermal/membrane hybrid (membrane distillation (MD) separation), chemical precipitation and stimuli-responsive (e.g., heat, magnetic field) separation.
3.1.1 Thermal separation.
Thermolytic salts, such as SO2 and NH3–CO2, have been proposed as draw solutes, because they have higher vapor pressures than the vapor pressure of water, and can be separated from draw solutions by a low-temperature distillation process. NH3–CO2 is the most studied thermolytic draw solute. NH3–CO2 draw solution can be formed by dissolving NH3 and CO2 gases in water at appropriate proportions, generating a high osmotic pressure.74 The ammonium salts are decomposed upon moderate heating (∼60 °C) into NH3 and CO2 gases, leaving behind product water. The separated gases could be re-dissolved into water for reuse. Low-grade heat, such as waste heat from power generation plants, could be utilized to separate draw solutes and enhance the system energy efficiency. Recently, a US patent revealed that a thermo-responsive osmotic solution comprises a tertiary amine containing compound, such as acetone/tertiary amine, which has a lower critical solution temperature in a solvent suitable for use in osmosis.75 The compound is immiscible with the solvent at or above 20 degrees Celsius and at 1 atmosphere. However, there are some drawbacks for these draw solution systems, including the high reverse solute flux due to the relatively low molecular weight and the deteriorated quality of product water due to the difficult removal of the draw solute residue from product water. To overcome these drawbacks, switchable polarity solutes, such as trimethylamine (TMA)–carbon dioxide, have been explored. Switchable polarity solutes can have phase transition from water-miscible to water-immiscible upon the presence of CO2.76 However, the study of switchable polarity solutes is still preliminary and toxicity concerns may limit their industrial applications.
3.1.2 Membrane Separation.
Due to their high osmotic pressure, inorganic salts, such as NaCl, MgCl2, MgSO4 and Na2SO4, were frequently studied as draw solutions. Researchers have considered conventional RO, NF and UF membrane filtration for the regeneration of these inorganic salts from diluted draw solutions. When monovalent salts (e.g., NaCl) are used as DS, RO is a good candidate for DS regeneration, given the low molecular weight cut-offs and high solute rejection of RO.71 However, it is widely accepted that the FO–RO hybrid process does not minimize energy consumption for seawater desalination compared with RO alone. In comparison with RO, NF is considered to have a looser membrane with relatively high molecular weight cut-offs, and can have higher water fluxes under the same applied pressure. An NF membrane is tight enough for retaining multivalent ions, with a divalent salt rejection of 99%. Tan and Ng72 investigated the NF recovery rate of a series of different DS (e.g., MgCl2, MgSO4, Na2SO4 and ethanol) after FO. Stable water fluxes of 10 L m−2 h−1) and rejection of up to 97.4% were achieved, with total dissolved solids (TDS) in the product water as low as 113.6 mg L−1 after a two-pass NF treatment process, meeting the drinkable water standard (TDS < 500 mg L−1) guided by the World Health Organization.86
UF membranes have a bigger pore size, which can be operated with lower pressure and lower energy, compared with RO and NF. UF can be used for the regeneration of the DS with big sizes (such as macromolecules, polyelectrolytes, or particles). For instance, Ge et al.73 adopted UF to recover the diluted draw solution of sodium polyacrylate (PAA-Na) (MW of 1800 Da). However, these draw solutes with big sizes normally have lower osmotic pressure and smaller diffusion coefficients into the membranes, which result in lower FO water flux.
3.1.3 Thermal/membrane hybrid separation.
Membrane distillation is a thermo-driven membrane separation process. In the MD process, the water vapor on the side of the hot feed solution diffuses across a hydrophobic porous membrane into the side of a cold solution, whilst retaining solutes on the side of the hot feed solution.87 The MD process has demonstrated many advantages over pure pressure-driven membrane processes, such as higher salt rejection, lower operating pressure, lower sensitivity to the osmotic pressure of the feed solution, and the potential to use low-grade thermal sources to heat feed solutions. For instance, Ge et al.77 investigated an FO–MD hybrid system for the draw solute regeneration of poly(acrylic acid) sodium (PAA-Na) salt. To date, there are still some drawbacks for MD to overcome including low water flux, membrane scaling and heat loss. In an alternative way, FO can be considered as a pretreatment step to remove organic and divalent minerals to mitigate fouling or scaling for the MD process, while it is purely in charge of separating water and draw solutes using low-grade heat.88
3.1.4 Chemical precipitation.
The solubility of some multivalent inorganic salts, such as Al2(SO4)3, CuSO4 and MgSO4, can be adjusted with pH change. Once these inorganic salts are precipitated out from the solution, fresh water can be produced, and the precipitate can be re-dissolved with an acid and reused. For instance, Al2(SO4)3 was used as a DS by Frank in 1972.78 After the FO process, the diluted Al2(SO4)3 solution reacted with calcium hydroxide (Ca(OH)2) to generate aluminum hydroxide precipitate and the product water after filtration. The precipitate was then re-dissolved with sulfuric acid to regenerate the Al2(SO4)3 solution and insoluble Al(OH)3 for reuse. In 2011, Liu et al. proposed a system of Al2(SO4)3 and magnetic nanoparticles as the DS,79 which can be separated by a magnetic field to produce fresh water. However, the health and environmental impacts of the chemical residue that remained in the product water are of concern for the practical application of chemical precipitation.
3.1.5 Stimuli-responsive separation.
With the purpose of finding a draw solute that could minimize the energy required for regeneration, some researchers have tried temperature, pH, or magnet-responsive draw solutes, including hydrogels, ionic liquids, and hydrophilic magnetic nanoparticles in the FO process. Stimuli-responsive hydrogels are polymers that undergo gel-to-solution phase change under an external stimulus, such as temperature or pH. The hydrogels take up or release water as they transition between different phases. For instance, Cai et al.81 studied thermo-responsive hydrogels based on polymerized N-isopropylacrylamide (PNIPAM) with polyvinyl alcohol (PVA) and polysodium acrylate (PSA). The semi-interpenetrating network (semi-IPN) hydrogels draw water through the membrane and release almost 100% of the adsorbed water at the temperature of 40 °C. These hydrogel DS have negligible reverse solute flux. Recently, Ju et al.82 presented a thermo-responsive poly(ionic liquid) draw solute, poly(4-vinylbenzyltributylammonium hexanesulfonate), which has a lower critical solution temperature (LCST) of ∼17 °C and can be recovered from the aqueous solution by heating it to above its LCST. However, the high viscosity of these polymeric draw solutions makes pumping of the draw solutions difficult, and the water flux in FO is relatively low due to the relatively low osmotic pressure of these draw solutions. Therefore, the physicochemical properties of these polymers need further optimization for their practical applications.
Nanoparticles functionalized with highly water-soluble and high ionic-strength groups have been tried as a promising DS, because of their easy separation under a magnetic field. Ge et al.80 coated magnetite (Fe3O4) nanoparticles with PEG diacid (PEG–(COOH)2. The nanoparticles have sizes between 4.2 and 11.5 nm. There are still some problems faced by using these magnetic nanoparticles, for example, the aggregation of nanoparticles leads to the decrease of osmotic pressure in the draw solution and subsequently impaired FO performance.
3.2 Draw solutions without the need for regeneration
3.2.1 Direct use.
A second step to regenerate draw solutes and produce pure water after the FO process is normally energy and cost-intensive. As a result, scenarios where draw solution regeneration is not needed could be more economical and practical. The FO processes without DS regeneration have been explored for the purpose of drinking, fertilization, irrigation and soil erosion prevention. Glucose was used as a draw solute in emergency packs, where the diluted draw solution is drinkable.89 However, the product water is sweet water, which is unsuitable for long-term drinking. Another scenario where no regeneration of the draw solution was needed was the use of concentrated fertilizer solutions as draw solutions. In this FO process, the fertilizer-based draw solution with high osmotic pressure can draw fresh water from wastewater or seawater, where the diluted draw solution can be used for fertigation. Phuntsho et al.84 demonstrated conventional inorganic fertilizers as DS, with 1 kg of fertilizer capable of taking up 11–29 L of fresh water from seawater. However, the concentration of the used DS is still too concentrated for the direct irrigation of crops, requiring further dilution with fresh water. Duan et al.90 proposed to use sodium lignin sulfonate (NaLS) as a DS in FO, and the diluted NaLS draw solution can be directly used for desert regeneration, by preventing soil erosion as a soil stabilizer, and simultaneously providing nutrients for plants.
3.2.2 Disposal.
Another economic option for the FO process without draw solution regeneration is the discharge of diluted draw solutions to where the original draw solutions come from. The draw solutions include high-salinity waters, such as brine from seawater desalination plants, or oil/gas produced water, which need to be diluted before environmental discharge. Adham et al.85 have demonstrated that the forward osmosis process was used to reduce the injection volumes of oil/gas field produced water, using desalination brine as the draw solution. In this process, the brine from desalination plants was used as the draw solution, which draws fresh water from produced water and concentrates produced water. In this case, the energy-intensive step of DS regeneration could be avoided, and the diluted DS could be simply discharged into the sea. One of the main challenges for this process is FO membrane fouling if raw industrial wastewater or seawater was used; however, this issue could be mitigated with effective pretreatment.91 Compared with seawater, the brine of desalination plants has some advantages as the draw solution: it has already been pretreated, it has higher salinity which translates to higher water flux, and it has an environmental benefit since the salinity of the brine would be reduced before disposal to the ocean environment.
4. Fouling and its mitigation in forward osmosis
Membrane fouling is an undesired complex phenomenon that is caused by the deposition of various types of organic and inorganic molecules/particles leading to the loss of membrane performance and efficiency.92 Adsorption of solutes/colloids and deposition of floc on the membrane surfaces and pores as well as formation of cake layers are among the fouling mechanisms that take place in a membrane.93 Fouling adversely affects the membrane selectivity, contributes to the loss of permeate flux and quality, and decreases the life span of membranes.94 It also leads to higher operating and maintenance cost as fouled membranes require frequent cleaning cycles. As shown in Fig. 5, the common governing factors of membrane fouling are (i) membrane properties, (ii) operating conditions, and (iii) feed water quality. There are many instances where fouling propensity is exacerbated by the combination of these factors.
 |
| Fig. 5 Three major governing factors of membrane fouling.95 | |
Fouling in membranes can be broadly categorized into three different groups as shown in Fig. 6. They are: – (i) inorganic fouling, (ii) organic fouling and (iii) biological fouling. Inorganic fouling, which is commonly referred to as scaling, is caused by the precipitation of inorganic salts and metal hydroxides.96 Scaling exacerbated by concentration polarization is a critical issue in NF and RO membranes, which usually deals with the removal of divalent and monovalent ions. As for the FO membrane, silica-scaling resulting from the polymerization of silica is one of the common inorganic foulants that hamper its performance. Organic fouling, on the other hand, is caused by the presence of natural organic matter such as polysaccharides, proteins, and fatty and humic acids in the feed water. This directly implies that organic fouling is likely to be the most dominant foulant in wastewater treatment systems. The adsorption of these organic compounds on the membrane led to the formation of a gel-like layer that increases the flux resistance.97 The presence of organic fouling and biological fouling can be directly interlinked and correlated in the majority of fouling cases as organic substances act as precursors of biofouling.94 Biofouling, which is defined as deposition, growth, and metabolism of bacteria cells or flocs on the membranes, is usually difficult to mitigate due to the protective extracellular polymeric substance layer.
 |
| Fig. 6 Common types of membrane fouling. | |
In general, it is well-known that the impact of fouling on the performance of a forward osmosis membrane is less severe than on a reverse osmosis membrane due to its osmotic driven process. The low operating pressure of FO membranes plays a key role in lowering fouling tendencies as it helps to minimize the deposition of foulants and reduces cake layer compression. Yu et al. reported that the reduction in flux of the RO membrane was nearly twice that of the FO membrane.98 Biofouling layers formed in FO membranes are generally looser than layers formed in RO membranes.92 Due to the loose attachment, biofouling can be sheared off from the surface of membranes. Despite their lower fouling tendencies resulting from minimal operating pressure, FO membranes are still susceptible to fouling governed by membrane properties and poor feed water quality. A comparison between CTA and TFC polyamide FO membranes by Wang et al. showed that the CTA membranes have a higher biovolume and thinner biofouling layer. They concluded that CTA FO membranes are more prone to biofouling, while TFC-based FO membranes are more susceptible to inorganic fouling. As FO membranes have higher fouling tendencies due to organic and biological fouling, the subsequent section outlines the common mitigation strategies used to address these two issues.
4.1 Organic fouling and biofouling and mitigation strategies
The mitigation strategies deployed in minimizing organic and biofouling in FO membranes are shown in Fig. 7. The common methods are as follows: (i) physical cleaning and process modifications, (ii) pretreatment, (iii) chemical cleaning and (iv) development of novel materials to minimize biofouling.
 |
| Fig. 7 Organic fouling and biofouling mitigation methods in FO membranes. | |
4.1.1 Physical cleaning and modifications.
One of the common approaches in alleviating the impacts of organic fouling and biofouling is via a physical approach such as using high cross-flow velocity to shear off the fouling layer from the surface of FO membranes. Mi et al.99 conducted a series of experimental studies to evaluate the reversibility of organic fouling in FO membranes using the cross-flow velocity approach. The recovery of flux in FO membranes fouled by alginate was evaluated using two cleaning cross-flow velocities (8.5 cm s−1 and 21 cm s−1), with flux recovery of over 98% achieved within 15 minutes of cleaning at a cross-flow velocity of 21 cm s−1, while it took 24 hours of cleaning to achieve a flux recovery of 96% at 8.5 cm s−1. These findings confirmed that the improvement in flux after cleaning is due to the removal of foulant by the shear forces induced by the cross-flow velocity. Another study100 investigating the effect of cross-flow velocity on the flux decline due to fouling confirmed that reduction of cross-flow velocity from 24 cm s−1 to 6 cm s−1 led to a 43% drop in the membrane flux. This study also reported that operation at higher cross-flow velocity also prevents additional flux decline over the long run of operation. It was suggested that higher velocity helps in preventing the accumulation of foulant on the membrane surface. Lofti et al.101 claimed that cross-flow velocity affects the concentration polarization and mass transfer near the membrane surface which in return governs the rate of fouling in membranes. For instance, thicker and rapid formation of biofouling can be expected at lower cross-flow velocity due to the reduction in mass transfer and increase of concentration polarization.
Researchers have also investigated other physical cleaning methods to control biofouling in FO membranes. Lee et al.102 noted that the usage of ultrasound radiation for fouling control in the forward osmosis sludge dewatering process is not feasible as ultrasound aggravates the fouling potential by releasing the organic content from sludge flocs which eventually formed a denser fouling layer that hampers permeation flux. However, they reported that when ultrasound was used in conjunction with higher cross-flow velocity, a synergetic effect can be observed, with high flux recovery after cleaning (73%). Lee et al.103 employed an intermittent pressure-assisted forward osmosis (I-PAFO) method to control organic fouling in TFC FO membrane coupons. By constantly inducing pressure relaxation on the membrane to manipulate the back transport of the foulant to the bulk solution, the authors were able to maintain higher water flux. Another popular method in mitigating organic and biofouling in FO membranes is by using gas bubbles. The presence of gas bubbles in the water flow can enhance the cleaning efficiency by increasing the overall shear force and turbulence. Du et al.104 investigated the impact of bubbly flow in addressing biofouling formation in a FO membrane used to treat wastewater. It was found that biofouling formation was uniform at an air sparging rate of 0.4 L min−1. They also reported that the drop in water flux was lower in bubbly flow and the presence of air bubbles minimized the buildup of biofouling of higher molecular weight. Fig. 8 shows the positive effect of using air bubbles in addressing fouling issues in FO membranes. Valladares105 investigated the impact of different spacer thicknesses (28, 31 and 46 mil; 1 mil = 0.025 mm) on the formation of biofilm in a FO membrane. They concluded that thick spacers could decrease the accumulation of biomass in the FO membrane.
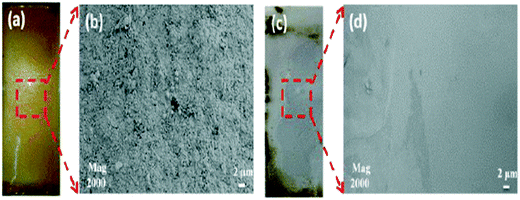 |
| Fig. 8 Impact of air bubbling in cleaning FO membranes106 (a and b – without air bubbling; c and d – cleaned with air bubbles). | |
4.1.2 Effective pretreatment.
Another option to minimize fouling issues is by having suitable pre-treatment systems. Pramanik et al.107 evaluated the performance of ultraviolet/persulfate (UV/PS) oxidation as a pre-treatment process for FO membranes that were used to treat anaerobically treated dairy effluent. The study showed that a higher flux, superior water recovery of 98%, and significant reduction in the deposition of reversible and irreversible foulants were observed when using UV/PS as a pretreatment process. Another study by Pramanik et al.108 assessed the efficacy of the ferric coagulation/persulfate (Fe/Ps) pre-treatment system in minimizing organic fouling in the FO membrane that was used to treat municipal wastewater. They observed 99% flux recovery after the Fe/Ps pre-treatment where this chemical combination was able to degrade humic acid and fulvic acid-like molecules. The efficacy of electrocoagulation in mitigating fouling in FO membranes was studied by Al Hawli et al.109 By using an aluminum electrode at a current density of 10 mA cm−2, they were able to remove 91% of total organic carbon and 97% of oil and grease from the simulated highly saline produced water. The combination of the electrocoagulation–FO membrane was able to remove total suspended solids and turbidity by 99% and 98.2%, respectively. Apart from coagulation and oxidation processes, adsorption can also be used as a pretreatment for FO membranes. Aftab et al.110 compared the performances of biochar and powdered activated carbon in mitigating the fouling of FO membranes from landfill leachate. The study concluded that by adding appropriate dosages, both biochar and powdered activated carbon were able to improve the filtered volume and flux recovery by 57% and >80%, respectively.
4.1.3 Chemical cleaning.
Although hydraulic shear is known to minimize fouling deposition, this approach could not completely remove biofouling. Yoon et al.111 reported that the flux recovery was insignificant in their FO cleaning studies when the cross-flow velocity was increased from 4 cm s−1 to 33 cm s−1. It was reported that a large number of bacteria still remained on the membrane despite the high cross velocity cleaning. However, the flux was completely recovered with the dosing of 100 mg L−1 chlorine at a similar cross-flow velocity. They concluded that chemical cleaning in combination with the shearing force is effective for the mitigation of biofouling in the FO membrane. Gao et al.112 made a similar conclusion where sodium hypochlorite (chlorine solution) is effective in controlling biofouling in FO membranes. They stated that by circulating 1% sodium hypochlorite for a period of 30 minutes, the water flux of the membrane could be restored to more than 96% of the initial water flux. Valladares et al.113 evaluated the performance of a chemical cleaning solution that consisted of 0.8% of sodium EDTA and 1% of Alconox (detergent) in cleaning the active and support layers of their FO membranes. It was concluded that this solution was able to remove a vast majority of transparent exopolymer particles from the FO membranes with a fouling reversibility of over 93.6% within 10 minutes of cleaning. Wang et al.114 reported that the performance of fouled polyamide TFC-FO membranes used in the operation of novel microfiltration (MF)-assisted AnOMBR (AnMF-OMBR) can be restored to achieve a similar performance to that of a virgin membrane by cleaning the fouled membrane using 0.5% hydrogen peroxide for 6 h.
4.1.4 Development of novel materials for fouling mitigation.
In recent years, significant effort has been put into developing novel and innovative membrane materials to mitigate fouling in forward osmosis membranes. Xu et al.115 developed a conductive thin film nanocomposite forward osmosis (TFN-FO) membrane blended with carbon nanoparticles to control fouling by manipulating the electrostatic repulsion between the foulant and surface of the FO membrane. They claimed that 4% carbon blending yielded the best performance with a corresponding water flux of 14 L m−2 h−1. By applying a voltage in the range of −1.7 V to 1.7 V, the water flux was improved by between 7 and 13% during organic fouling studies. Fan et al.116 developed an electrically assisted FO process using carbon nanotube hollow fibers to improve the fouling resistance in a TFC FO membrane. This study reported that at an applied voltage of 2 V, the flux of the electrically enhanced membrane was consistent throughout the operation, hence suggesting the organic fouling can be effectively mitigated using this process. In addition, the study also claimed that the fouling potential due to humic acid and E. coli is lower in the developed membrane as the repulsive force between humid acid and the cathode membrane can be increased by applying sufficient voltage. Another study117 reported the usage of a zwitterion–silver nanocomposite (ZTFC–Ag) structure to modify the FO membrane surface with an aim of improving the membrane transport, antiadhesive and antimicrobial properties and hydrophilicity. The modified ZTFC–Ag membrane demonstrated excellent antimicrobial properties where only 4% of E. coli was found on the membrane after the filtration process. The membrane also recorded the lowest flux decline of 8% when compared to other membranes tested under similar conditions. Faria et al.118 developed an anti-microbial FO membrane by functionalizing TFC membranes using graphene oxide–silver (GO–Ag) nanocomposites. The developed membrane was excellent in inactivating Pseudomonas aeruginosa cells by 80% while also reducing the total protein mass on the membrane by almost 50% to 6.2 pg μm−2. This study also reported that the GO–Ag functionalized TFC membrane was capable of reducing biofouling formation by 30%. Another interesting study utilized a re-generable polyelectrolyte to mitigate fouling in FO membranes.119 In the event of irreversible fouling, the sacrificial polyelectrolyte substance could be released under controlled conditions and eventually regenerated in situ to resume the membrane functionality. It was confirmed in this study that the regenerated membrane produced a similar water flux to the pristine membrane.
5. Recent developments and niche applications
There is increased global focus on water sustainability and focus on recycling and reusing produced water is gradually coming to the forefront of the agenda of the oil and gas industry. Water scarcity and water security issues are intrinsically related to the adverse environmental impacts of injecting produced water into disposal wells. These recent trends are a reflection of the need for produced water management including a fundamental improvement and subsequent implementation of these treatment technologies.120 Independent research across the world in recent years has covered the novel application of forward osmosis technology to minimize the volumes of produced water generated for injection into disposal wells. This research has an impact on a global scale and is important in areas where there is increased oil and gas activity.
Forward osmosis-based technology applications cover a wide range of fields in industry that include bench-scale laboratory experiments and full-scale pilot demonstrations. Some of the practical uses of FO that are covered within this section range from the food and beverage industry, pharmaceutical and juice concentration, wastewater reclamation, brackish water/seawater desalination, fertigation in agriculture, zero liquid discharge (ZLD) concept and finally industrial scale-up and other industrial processes.121,122 Depending on the application, implementing FO may have a detrimental effect on operational power requirements. In recent years, improvements in FO systems, including draw solution testing and membrane material development, have enabled the production of more flux whilst reducing the occurrence of the bane of membrane-based technology, internal concentration polarization, thus improving energy requirements and fouling effects.
There is huge potential for FO to be used as both an independent and a hybrid system, in conjunction with other existing technologies. Some of the applications for utilizing the benefits of forward osmosis include the food and beverage industry, chemical industry, coal processing, textile industry, pulp and paper industry, pharmaceutical industry, electronic industry, micro algae cultivation and car manufacturing, amongst many others. There have also been a number of peer reviewed FO publications about heavy metal elimination and cooling water treatment that have been identified and reviewed. The up-scaling to pilot or full-scale will be the essential next step for many of these processes and their reliability will depend on a number of factors including membrane performance, new methods for draw solution and feed solution regeneration, etc. Long-term fouling behavior, membrane cleaning methods, and operation procedures are also very important parameters that will need further assessment studies.
5.1 Desalination & wastewater treatment
The increasing frequency of water shortages around the world coupled with strict environmental policies in many countries and the movement towards sustainable development and the increasing demand for available freshwater resources make the ZLD technology a valuable wastewater treatment option. It is an important strategy for sustainable management of wastewater. There has been substantial investment in ZLD technology. Forward osmosis has increasingly become an attractive salt concentrating technique.123
The forward osmosis system has been shown over time in various research studies to work effectively for the rejection of different pollutants and recovery of nutrients from various types of wastewater. The results from Chen et al. confirmed that using concentrated sewage could replace the anaerobic digestion feed and produce a high quality final effluent. However, there are still problems that need to be addressed to make the FO process practical for deployment in this particular area.124
In recent years, a number of hybrid FO systems have been incorporated into existing or combined processes for various applications including seawater/brackish water desalination and wastewater treatment to replace conventional pre-treatment technologies or as post-treatment to reduce the extra volumes of industrial waste. The combination of FO and RO in a hybrid process, where FO uses a wastewater stream to produce high-quality water to dilute seawater prior to an RO step, is very feasible. In another study as documented by Pan et al., a forward osmosis–membrane distillation hybrid process was utilized to remove tetracycline from wastewater, with a rejection of 99.9% and a water recovery of 15–22%.125 In addition to water recovery, FO can be used in wastewater treatment for nutrient and energy recovery.8
Some of the very useful applications of forward osmosis are the added value of integrating seawater desalination and municipal wastewater treatment to produce a much cleaner water product. This technology has shown relatively high rejection rates for many variables being monitored at treatment plants including COD, phosphate, trace metals and an average rejection rate for ammonia and total nitrogen. Forward osmosis has also proven to be a very reliable barrier in the rejection of a host of contaminants and salts found in wastewater that can be utilized as the feed solution or in seawater as a draw solution. The combination of municipal wastewater treatment and seawater desalination creates the added benefit for a considerable and sustainable energy-saving approach to a more sustainable urban water management and water reuse strategy. One of the main drawbacks in desalination technology is related to separation and recovery of the draw solution from the desalinated water. The successful implementation of forward osmosis related desalination in subsequent years will be reliant on the effectiveness of the draw solute recovery from desalinated water. Some of the industrial applications are detailed in Fig. 9.
 |
| Fig. 9 Niche industrial applications of the FO process. | |
Research has also been carried out using FO membranes with secondary wastewater effluent utilized as feed water and seawater as a draw solution, with results showing huge strides and indicating that the technology is encouraging. Indirect desalination using a hybrid system comprising forward osmosis/low-pressure reverse osmosis (FO/LPRO) has also been implemented, which requires only half of the energy used for normal high pressure RO desalination technology. The results show that very high quality product water can be realized from the feed.126 One of the most commonly utilized desalination technologies currently employed, especially in the arid gulf region, is seawater reverse osmosis (SWRO). Scaling up of a FO/LPRO system for several industrial applications, and in particular seawater desalination, has been investigated as a cost effective solution for producing fresh water and minimizing fouling problems. The low energy requirements that are needed to remove water from the feed solution make forward osmosis a very attractive technology solution.127
A working experimental procedure was developed in the laboratory for a novel “single-step” forward osmosis process concept where reject brine from thermal desalination plants was used as the draw solution to separate clean water from produced water, hence reducing the total volume of water generated. It runs in an osmotic dilution method of operation which guarantees low energy consumption.128 It is also important to note that the process water realized is a mixture of offshore produced water and process water from onshore gas liquefaction operations. With regard to this application, one of the key advantages of the FO process over other conventional processes is the lower CAPEX and OPEX. The need for high pressure pumps is eliminated and this reduces electrical energy consumption.1,129 FO desalination processes have a unique collection of potential advantages if they are installed on a large scale and transferred to a commercial scale. The low hydraulic pressure that is commonly applied whilst running an osmotically-driven FO process is responsible for the added advantages. It is also synonymous with low energy consumption which drives down associated costs if the draw solution recovery step is economically and technically sustainable.13 FO membrane contactors can also be used to remove natural steroid hormones from wastewater.130 The basic concept for the desalination process involves two steps, the first is FO and the second is a recovery and separation step using RO. Researchers have laid claim to the fact that this process has lower energy consumption for desalination applications than a reverse osmosis plant coupled with advanced pre-treatment including ultra-filtration, when used to treat high salinity water. The RO step in the FO/RO combination operates at much higher recovery ratios than in a single RO step.
In this particular study, a novel module design to integrate forward osmosis (FO) and membrane distillation (MD) was proposed and investigated with a view to using a FO–MD novel integrated system for domestic wastewater treatment applications. The FO–MD integrated module does not require additional pumps, pipes or an intermediate tank and other ancillary equipment to ensure the flow circulation in both modules.131 The integrated FO–MD system captures the complementary advantages provided by FO and MD in a single step. However, this hybrid system has a serious potential problem associated with the configuration having the FO DS and the MD FS flowing in the same channel simultaneously, that is, the same stream in contact with the MD and FO membranes. The newly proposed integrated module has two separate flow channels within the same module, separating the FO DS and MD feed streams using an isolation barrier inserted inside the module with an opening on the top, allowing the MD brine (MD outlet) to flow in the FO DS inlet side. This feature makes the integrated module osmotically and thermally isolated, which ultimately increases the efficiency of both processes. However, the FO–MD hybrid can compensate for the individual weakness of FO and MD membranes and hence enhances the rejection of all contaminants.132
The higher performance of the proposed integrated module will reduce the required membrane surface area compared to the typical integrated module. In order to evaluate the novel FO–MD integrated module, a number of iterations and investigations were carried out based on mass balance equations varying four different parameters: FO and MD recovery rates, initial DS flow rate, and initial DS concentration. The results showed that a high DS flow rate was a prerequisite for a high recovery rate in the FO–MD integrated module. The results and findings from the simulations show that the novel FO–MD integrated module can have very beneficial use for small-scale or mobile water and wastewater treatment plants. A very good example of the application of the integrated module is the treatment of hypersaline wastewater from shale gas fracking due to easier membrane fouling control and high rejection of volatile compounds and other toxic metals.
5.2 Water reuse
FO membranes across various applications were tested and investigated to determine their ability to reject a wide array of organic micro pollutants. The rejection rates across these investigations yielded values within the range of 40% and 95% for hydrophilic neutral compounds and hydrophobic neutral contaminants but were significantly higher, up to 99%, for hydrophilic ionic micropollutants. A hybrid system of FO and LPRO has also shown high efficiency in rejecting low molecular weight hydrophilic neutral micropollutants, with greater than 89% rejection. A hybrid FO/LPRO system also acts as an effective obstacle against micropollutants, including pharmaceuticals, hormones and other micro organic pollutants.127 Forward osmosis has been adapted as an osmotic dilution process using seawater as the draw solution for water purification within a hybrid FO/RO process.133 There are other configurations of FO/RO desalination systems that have been proposed to generate both potable water134 and the osmotic power of brine from RO. Within these dynamic configurations, FO gives high quality drinking water as a result of the double layer protection, reduced RO fouling via pretreatment, recovery of osmotic energy of RO brine, reduced energy consumption and no pre-treatment requirements.
5.3 Produced water treatment & enhanced oil recovery
Collaborations between two companies, Bear Creek Services and Hydration Technology Innovations, LLC, with respect to treating wastewater being generated from oil & gas operations to assess the reliability of forward osmosis as a viable technology to treat drilling fluids from shale gas operations showed a high recovery value of around 90%.135 Oasys Water Inc. was another company that carried out a feasibility study and assessed the use of forward osmosis as a technology option to treat flow back process water from shale gas operations using ammonium carbonate as a draw solution. Some of the results showed an average of over 60% reduction in volume of water.74 Bench scale investigations using forward osmosis for treating produced water was carried out on drilling fluid in shale gas operations where the reduction in the volume of water was up to 80%, with TOC rejection greater than 99%.136 The hybridization of forward osmosis and membrane distillation involved using an integrated FO–MD system for increased generation of process water from oily water mixtures. The combination of these technologies showed very effective treatment of oil and gas produced wastewater to produce potable water. This hybrid system had certain advantages that made it feasible to overcome many of the adverse effects of each process on its own function.137 In an RO–MD hybrid system, clean water is recovered from oily effluents using RO brine as the feed constituent. The diluted brine is regenerated so that it can then be reused as a draw solution and also to produce up to 90% water recovery with little or no organics in the effluent.137 Forward osmosis has been proved over the years via independent research by scientists and engineers as a viable option to treat high-salinity produced water. Forward osmosis is one of the few approaches considered to be a viable option to treat the high salinity of produced water solutions.138 However, there needs to be some form of pretreatment as a step before using forward osmosis as a remediation technique to reduce the tendency for fouling. It was concluded that forward osmosis could be used to extract high quality water from high-salinity oil field brines and produced water.139
5.4 District cooling
Forward osmosis is a technology that provides a low TDS make-up water supply to a recirculating cooling water system acting as an osmotic agent. The economics and robustness of the process are value added points to its implementation and practice; however, the relative emergence shows that it may take some time for the technology to be readily accepted by industrial stakeholders in this sector. The evaporative cooling process requires vast amounts of very high quality water to replace the water lost by evaporation, drift and consequently, blowdown. Desalination processes and the more recent utilization of treated sewage effluent, especially in Qatar and in other gulf countries, are the source of cooling and make up water. The recirculating feed water is processed into a draw solution and subsequently, the make-up water is pulled across a suitable forward osmosis membrane. There is contamination of the draw solution from ions, which are transferred across the forward osmosis membranes. The source of these ions is most likely the contaminants in the atmosphere. In order to retain the draw solution but filter out the target contaminants, a blow down recovery system is required and this has been developed and demonstrated.140
5.5 Agricultural irrigation/fertigation
Fertigation is an agricultural irrigation process that is employed on a wide scale where water soluble fertilizers are added to the irrigation water in order to improve and enhance crop yield. The concept of fertilizer drawn forward osmosis (FDFO) for fertigation has been offered as a viable option for reducing the volumes of potable and desalinated water used in the process. The most interesting finding related to this study was that the diluted draw solution could be directly utilized and applied to irrigation without the added step of separation.84 This process is an example of osmotic dilution and there have been investigations that have been carried out to evaluate the performance of fertilizer draw solutions using low energy fertilizer-driven forward osmosis desalination. Some of the issues that were realized in this application were the over concentration of the fertilizer after it has been diluted and the eutrophication of the receiving water body due to the presence of amounts of nitrogen and phosphorus. FDFO contributes to preserving fresh water supplies by reducing the volumes of desalinated water and fresh water used to dilute liquid fertilizer concentrates in the fertigation process. However, it is faced with quite a number of challenges which may hinder its large scale deployment as a viable technology.141
5.6 Dairy industry
The dairy industry uses raw milk to produce many food items including long-life milk, cheese, and yogurt, amongst others. Huge amounts of wastewater are generated from manufacturing and production as well as in situ and ex situ cleaning procedures and dewatering as investigated and documented.142 The recycling of wastewater within the industry is of huge concern and there have been a number of reviews on FO lab-scale experiments conducted using artificial whey solution generated using deionized water and whey powder. The economic implications of utilizing forward osmosis were also studied and assessed and conclusions were drawn on the basis that FO required a lot less energy and less space translating into lower overall costs.143 A hybrid FO/MD configuration was developed and assessed from a feasibility study using real dairy wastewater as the feed solution and sodium chloride as the draw solution with different FO membranes. The results were conclusive and proved that FO could concentrate real dairy wastewater under normal operating conditions and MD could obtain the desalted water at the end of the process.143 The optimum recovery of the draw solution for applications in the dairy industry is much easier than in the instances where products show up in the draw solution, with desalination as an example. In the production of fruit juices, milk and skim milk concentration, it is necessary to concentrate the feed stream and water goes into the draw solution but water is not important as a product. This is because the final product is actually the concentrated feed stream. This ultimately makes draw solution regeneration in dairy processing more practical and feasible than in the desalination process.
5.7 Chemical industry
FO technology shows potential for niche application in the chemical industry. Organic acids such as lactic acid144 or succinic acid produced by fermentation could be concentrated by FO treatment. Glucose has been examined as a draw solution, with a permeate flux of 12 L m−2 h−1, which corresponded to an 84% water recovery value. However, there was only 56% rejection of lactic acid. Several other researchers have primarily focused on using FO for the treatment of acids. In one of the studies, different carboxylic acids were concentrated by FO.145 These acids are utilized in many chemical processes. For this reason, they are likely to be contained in the wastewater from chemical production processing, and could be treated using FO.
5.8 Food processing
The use of forward osmosis technology in the manufacture of sugar drinks from a seawater and brackish water mixture has been explored and implemented and is amongst very few commercial applications developed for deployment in the US military.146 A sugar solution (dextrose and fructose) within a bag served as a semipermeable FO membrane where water gradually flowed through the membrane after dipping it into an aqueous suspension. It could then be utilized as an electrolyte energy drink. The use of much larger systems has been practiced in certain countries for disaster relief and emergency scenarios and conditions.147 The use of FO for the treatment of olive mill wastewater was also investigated using real wastewater rich in biophenolic compounds as the feed solution and magnesium chloride as the draw solution. These experiments were run continuously over a sustained period of time and the feed solution and draw solution were replenished on a daily basis. There was fouling as a result of the time taken for the experiments but pure water permeability could be restored to 95% via rinsing and osmotic backwashing. Various pre-treatment methods were tested with this configuration of FO treatment and it was found that microfiltration was the most effective method and subsequently increased the permeate flux of FO. Particle retention by microfiltration increased the FO permeate flux.148
5.9 Pharmaceutical industry
Within the pharmaceutical industry, the application and utilization of forward osmosis includes osmotic drug delivery and enrichment of pharmaceutical products as outlined in various publications.149–151 The osmotic drug delivery systems are based on the principle of osmosis and the second area relates to the enrichment of pharmaceutical products. These pharmaceutical products are heat sensitive and possess large molecules; this means that forward osmosis technology can bring some certain advantages that conventional methods will have difficulty with. FO was also applied to the concentration of anthocyanin and the results indicated that FO possessed many advantages over the alternative thermal concentration in terms of higher stability and a lower browning index.152 The enrichment of protein solutions using an integrated FO–MD system has also been assessed and investigated.153 It is worth noting that in the fields of food and pharmaceutical product concentration, the concentrates of FO are the target products, which is quite different from desalination and wastewater treatment. FO has also been demonstrated to be very effective for dialysis fluid regeneration.154
5.10 Electronics industry
The wastewater streams generated from the electronics industry usually contain valuable and precious heavy metals that may be toxic and pose significant risks. One example that was reported by Gwak et al. was the use of forward osmosis to treat wastewater from a printed circuit board manufacturer. Palladium containing wastewater was utilized as the feed solution and was concentrated up to 90%. It was also mentioned that the presence of inorganic fouling occurred on the feed side and hence, more investigations need to be had in order to make more valid claims regarding the effectiveness of this technology in this area.155
5.11 Challenges, limitations and drawbacks
Some key technical issues, which are related to the successful operation and implementation of FO technology in niche applications, still need to be addressed. Some of them are the ideal membrane material, a suitable draw solute and its recovery approach, the mechanism of the target wastewater, membrane-fouling mechanisms, cleaning strategies and protocols, which still exist as hindrances and barriers and need the focus of future research patterns. The following aspects of FO that need attention in order to fully optimize its application are shown below:156
a. The realization of high water flux
b. Low reverse salt flux (RSF)
c. High mechanical strength of the membrane
d. Low ICP film material modification and preparation
e. Special modification and preparation of properties or functional membrane materials
f. Development of new composite DS
g. The membrane fouling principle and fouling cake layer formation mechanism
h. The principle and solving methods of the accumulation of pollutants and salinity in the DS
i. Membrane fouling mitigation and membrane cleaning methods and strategies
j. The preparation uniformity of membranes
k. Preparation of the draw solutes applied to the appropriate field.
One of the biggest challenges that has been identified in the thermal desalination process is the issue of scaling, where the precipitation of salts like calcium sulfate and other sulfates and carbonates will lead to process issues and reduction in process efficiency in due course. Calcium sulfate, for example, precipitates above 115 °C, which limits the top brine temperature and has an adverse effect on the overall efficiency of the distillation process.157 A good example of a strategy to overcome this issue is combining membrane distillation (MD) and forward osmosis (FO) to desalinate water because it is difficult for the standalone MD process. When utilizing a hybrid FO–MD system, FO is used as a pre-treatment step to reduce organic fouling and/or inorganic scaling which usually has detrimental effects on the MD process over time.
There are a few limitations in the developmental phase of large-scale applications of forward osmosis technology. One of the main ones is the concentration polarization phenomenon, which reduces the osmotic pressure driving force and results in a much lower water flux value. More work also needs to be done to optimize the thermal desalination process and improve the overall process efficiency.
Internal concentration polarization (ICP) causes a drop in the concentration gradient created across the porous support layer, which lowers the osmotic driving force and effectively reduces the water permeability through the membrane.158 This effect depends primarily on the characteristics of the draw solution (DS), membranes and operating conditions employed during the FO process.159 The concentration polarization phenomenon due to the accumulation of solute on the surface of the membrane or in the pores is fouling. This happens and effectively reduces the overall membrane performance. It causes either the formation of a cake layer on the membrane surface or clogging up of the pores. This results in a very steep decline in water permeation, a reduction in separation efficiency of the membrane and a diminished hydraulic resistance.160
The financial and economic aspects of the need for an additional energy-consuming process, which is a post-treatment step to recover the draw solute, are considered as another drawback of FO for use as a standalone process.13 In terms of membrane development for use in FO systems, some of the drawbacks that were mentioned above must be overcome to achieve the successful installation of FO applications in industry. The issues of process problems associated with the development of the membrane should contribute considerably to the improved efficiency of the FO system.
The standard operation protocol for these modules are still hindered by membrane fouling and associated increased operational costs. After testing the membranes and carrying out performance tests, they became fouled and required cleaning and regeneration. However, there were no guarantees that the membrane would return to its original state. In the desalination process, high quality water is needed as the final product. Water goes into the draw solution and the final product needs to be extracted from the draw solution, but there are various challenges that need to be addressed in draw solution recovery. The energy consumption of forward osmosis will not be economically feasible because the draw solution is more highly concentrated than standard seawater.
The development of reliable and accurate predictive models to calculate energy expenditure is still one of the areas of focus that researchers can improve on. It is important to optimize the energy consumption of the well-established FO standalone system in comparison with the hybrid system to convert the process into a more feasible industrial application for water and wastewater treatment.
The impact of ICP on the FO water flux can be very severe, in some cases even leading to a water flux decrease of over 80%. It seems clear that there is still considerable uncertainty about the optimal support morphology for FO applications. Hydrophilicity is one of the parameters whose influence on FO performance has been extensively investigated. Not only does the hydrophilicity of the membrane support assist in wetting and water continuity within the membrane, it also mitigates ICP.
Developing a membrane with a low ICP is what is needed to improve the performance of FO technology. Modifying the membrane support layer is the correct option to explore since ICP cannot be controlled by fine-tuning the operational conditions of FO.161 As ICP is determined by support layer structure and hydrophilicity, a lot more research and development efforts should be carried out to improve those parameters.162
There are very specific research areas in forward osmosis that have some challenges and limitations related to wastewater treatment and they include the choice and nature of the draw solution, economic cost, the degree of efficiency of the regeneration process and the configuration and manufacturing process of the membrane. These are some of the factors that will need to be overcome to make the process more attractive on a large scale.
5.12 Benefits
In the applications that involve challenging feed water with high fouling potential, high salinity, or containing specific micro-organic contaminants, FO has been proven to be an effective technology as a pre-treatment step to improve the overall efficiency of conventional desalination processes. Due to the many advantages of forward osmosis including the low hydraulic pressure and low energy consumption, this economically feasible and technically sound technology has been widely investigated in the application of seawater desalination. It should also be highlighted that the FO stand-alone process can treat wastewater to produce either a concentrated wastewater stream or a diluted wastewater stream, depending on the resulting application of the effluent stream. Using the FO process for the removal of organic matter has proven to be very effective and can yield a sustainable, optimized and relatively inexpensive process.8
The enhanced water flux of the PAFO (pressure-assisted forward osmosis) process gives a lot of room for the greater dilution of seawater than the standalone FO process, which results in greater energy savings in the RO step. PAFO also uses a lower surface area of the membrane in its operations and performance, thereby giving an overall cost saving. PAFO has been shown in many instances to enhance water productivity, which is attributed to higher water flux due to the application of hydraulic pressure. This improvement resulted in reducing the membrane area required compared to FO.163
The advantages of FO as a standalone technology can be also applied to the treatment of wastewater with a high pollutant concentration. The water is drawn from the wastewater leading to the reduction of wastewater volume. Meanwhile, the pollutants are effectively rejected by the FO membrane. FO also offers up several advantages compared to other pressure-driven membrane processes, including the low pressure requirement and the ability to treat a high solid content solution.164 The low fouling tendency of FO is due to the low hydraulic pressure and low permeating flux resulting in non-compacted and reversible fouling. Among the alternative processes, FO offers several attractive features allowing addressing the drawbacks of the thermal energy-based processes. In addition to its ability to produce a final product with a high solid concentration, FO can retain the bioactivity of nutraceuticals due to its mild operating conditions.
5.13 Future trends and direction
Currently, forward osmosis is very well suited for niche applications where water needs to be removed using very gentle and precise methods. Some of these include food processing and concentration of valuable chemicals such as flavors & fragrances and pharmaceuticals. This technology will be particularly applicable in the future when smart draw solution systems become industrially available that will leverage on utilizing waste heat or solar thermal energy for draw regeneration (e.g. the membrane distillation hybrid process). In order to commercialize the FO process, it is important to recognize industrial applications where the most value generated for FO and the technical challenges faced by companies wishing to commercialize FO processes can be tackled and addressed accordingly. In this regard, the most pressing concern is where there is a high guarantee of implementation and where efficiency and return on investment are considered with a cost benefit analysis and economic assessment.
The growing trend in wastewater treatment on a global scale related to the removal of organic materials and pollutants of emerging concern (especially organic materials) could be expected to continue in the next few years, with environmental compliance being the priority in many countries. This validates the area of fouling resistant membranes, which can be of great interest to researchers in the future.
The recovery system for the draw solution is related to the overall FO system which is crucial for the effective implementation of FO. The recovery rate efficiency when treating actual contaminated water is also important for the feasibility of the full-scale FO system. The regeneration of the draw solution has seen a noticeable research activity over the last 10 years with an increasing number of publications in the area.165
The practicality of the FO process has been investigated and studied to enhance its efficiency by applying it to alternative hybrid processes such as FO–RO and FO–PRO. These hybrid processes have been shown to overcome some of the limitations from the standalone processes formerly employed. PAFO (pressure-assisted forward osmosis) has been proposed as an advanced concept for improving the performance of FO in applications related to agriculture and fertigation. The working concept of PAFO involves a hydraulic pressure that is directly applied on the feed side, where combined actions of osmotic and hydraulic pressures are used simultaneously as the driving force for water transport. This makes PAFO a well-equipped and enhanced technology to resolve one of the major problems associated with FO, which is low permeate water flux.
The additional hydraulic pressure within the PAFO process enhances the permeate water flux over concentration polarization and reduces reverse salt diffusion. PAFO can also be utilized in the FO–RO hybrid processes as the PAFO–RO configuration, since the low water flux of FO is still regarded as economically inappropriate for FO–RO processes due to its high investment and operational costs. In the FO–RO configuration, FO is used as a pretreatment step before RO, utilizing both secondary wastewater effluent as the feed water and seawater as the draw solution. This is used to dilute the seawater and save energy-related costs in the RO process.
One of the drawbacks of DS regeneration is the high energy consumption of pumping and high overall cost of the process which depends on the type of the used draw solution. However, the breakthrough is essential in the draw solution and regeneration system as these should be studied according to the overall system approach. A better understanding of the FO fouling mechanisms and fouling cleaning strategies will be beneficial for further application of FO. The main driving force of FO due to its membrane permeation process is osmotic pressure, different from UF, NF, RO, and other membrane filtration processes which require higher external pressure as the driving force, and membrane fouling is relatively light and easy to clean. However, membrane fouling remains a major drawback that cannot be ignored in FO systems. The FO membrane has shown promising prospects in both drinking water purification and wastewater treatment technology, especially its excellent high rejection rate performance and relatively low membrane fouling characteristics. Hence, it is likely to become a very important membrane technology in the future.
In the last 10 years, a large number of research papers focusing on FO have been published and the number of papers in various issues has increased year by year, especially in the issues of the draw solution and the membrane material.160,166 The engineering of the forward osmosis process application and technologies is relatively scarce as a lot of the FO research is currently on the laboratory scale, with some progress in practical applications. However, there is still room for pilot scale trials and proof of concept studies. The advanced strategy of chemical cleaning remains to be further researched and developed.
FO membrane geometry should be chosen wisely in accordance with the intended application. Particularly in treating highly viscous solutions or solutions with a high solute loading such as in the food industry or in wastewater treatment, a hollow fiber geometry is preferred over flat sheet-based (spiral wound) membranes. It is well established that the hollow fiber geometry has a low fouling tendency, suitable for these applications. Widjojo et al. showed that the support's hydrophilicity had a greater impact on FO performance than morphology. They managed to fabricate supports with different morphologies and degrees of hydrophilicity by changing the amount of sulfonated material in the membrane support. Interestingly, the sponge-like more hydrophilic structure produced the best results in FO.47 The ICP can be determined intrinsically and empirically, and each of these approaches has its shortcomings. More work is needed to find an accurate method and universal testing conditions to estimate the ICP. Only this will allow a proper development of the next generation of supports for FO membranes.167
5.14 FO, agriculture and food security
Agriculture is by far the largest consumer of freshwater, accounting for almost 80% of water consumption worldwide. Energy-efficient desalination techniques could be a promising way for providing water for irrigation. Pressure-assisted forward osmosis (PAFO) has been recently introduced in a recent FDFO study. PAFO could potentially eliminate the need for further post treatment. In fact, the additional water flux generated in the process can enhance the final fertilizer DS dilution beyond osmotic equilibrium making the final product water suitable for direct fertigation.7,168
FDFO desalination is not only energy efficient, but it also improves the efficiency of water and fertilizer applications. However, the major limitation of the FDFO process is its environmental compliance with the irrigation water quality standards in terms of nutrient concentrations, which limit the use of the product water for direct fertigation. This is an area where policy makers across the world have to use science-based research to drive the guidelines for proper use of the technology.
In the food industry, a very critical process step is to dewater liquid foods to improve product stability as well as to minimize packaging, storage, and transportation costs. The most common technique used in liquid food concentration is vacuum evaporation, but the high temperature applied in this technique results in the degradation of temperature-sensitive components such as vitamins, flavor molecules and phytochemicals.169,170
FO's low fouling tendency is also a big benefit in the food industry in which major fouling of the membranes can be expected.171 Inherently, a dewatering step aims at a high overall recovery, or a high concentration factor. This means that, similar to wastewater applications, hollow fiber or tubular membrane geometries are preferred. FO showed almost 7.5 times higher rejection of urea as compared to the RO rejections. The operations in FO mode typically showed a better performance in rejecting small solutes such as urea and micropollutants than operation in RO mode. This makes FO also interesting for applications where small solutes need to be removed on a large scale.
A concentrated solution of the intended fertilizer is used as the draw solution for the desalination of either brackish groundwater or seawater. The advantage of this process is that the diluted draw solution would not require post-treatment to re-concentrate the draw solution.172 Another way to evaluate the potential of fertigation is to evaluate the relative amount of brackish groundwater that FO can contribute relative to other sources of irrigation water. The more brackish groundwater that can be utilized via FO treatment decreases the water usage from other sources. Ultimately, the potential utilization of brackish groundwater depends on the feed water osmotic pressure and draw solute, which dictates the required dilution necessary prior to application.
The promising aspect of fertigation is that it presents an FO application where concentration and recovery of the draw solute is not a primary concern. The disadvantage, however, is that the draw solute concentrations needed for practical fluxes generate a diluted draw solution that is still too concentrated for direct application to crops. The dependence of extraction capacity (and diluted draw solution concentration) on feed solution osmotic pressure limits the potential feed sources where this technology may be viable. From a practical standpoint, the feed solution likely has to have an osmotic pressure less than 5 atm and be pre-treated with an NF process, if the FS salts have divalent cations, for any substantial gains from implementing an FO process to be realized.
The rationales behind FO treatment of each application vary. The direct use of the diluted draw solution is promising for fertigation FO, but significant dilution prior to agricultural application likely limits the practicality of implementing FO without a low salinity water source for dilution or another treatment process. FO is a potential treatment alternative for highly saline brines for minimizing volume and recovering water. This technology may have a niche, because pressure-driven processes are not feasible as salinity increases. Identifying uses for the diluted draw solution, however, remains imperative. Ideally, brine waste minimization would be highly favorable if there was a direct use for the diluted draw solution or draw solute recovery did not include membrane processes.
If the original brine is hazardous, concentrating the hazardous material prior to shipping or disposal may yield large cost benefits despite treatment needs of the diluted DS. For desalination and water reuse applications, a benefit from FO is water transferred from a feed solution with high scaling or fouling potential to a solution with low potential so that membrane processes can operate at higher recoveries.
For FO to move from bench scale to full-scale applications, more focus on identifying specific niches where FO makes both economic and practical sense compared to more conventional treatment processes is required.
5.15 Forward osmosis – commercial applications
Over the last four years, the emergence and growth of the FO market and landscape have changed. Back in 2015, BlueTech173 published a report on FO, where there was a lot of research and development, with an emphasis on commercialization around the technology, but there were some difficulties associated with achieving full commercialization. The FO market in its current stage and status now covers a varied spectrum from the ZLD market which was worth approximately $300 million in 2017 to a record of around $6 billion taking into account product concentration, ZLD and water reuse, amongst others. The market is dominated by FTSH2O, Porifera, Oasys and Modern Water. However, the FO market is small. None of the companies have more than a few commercial installations. FO as a technology is gaining market traction in ZLD/brine concentration, production of valuable products by dewatering, minimizing waste hauling costs, concentrating difficult to treat wastes, landfill leachate treatment and specialized desalination opportunities. Within the next five years, FO will likely be picked up by larger firms as a product offering within a suite of water treatment, brine management and water extraction solutions. The evaporator market will be more challenged by FO, but the FO addressable market will be more realistic than today's most optimistic projections. Table 2 shows the commercial entities that provide FO technologies for various applications.
Table 2 A list of commercial entities that provide FO technologies165
Company |
History |
Industrial applications |
Application Status |
Location |
Nature of Business |
Forward Water Technologies174 |
Independent company specializing in the commercialization of forward osmosis technology. Founded in 2012 |
Large-scale implementation of its technology in industrial wastewater, oil and gas, mining, agriculture and water supply and re-use |
Fully commercialized |
Canada |
Revolutionizing the remediation of wastewater |
https://forwardwater.com/
|
Sterlitech Corporation175 |
Founded in 2001. Its founders have over 90 years of combined experience in membrane and microfiltration technology |
Sterlitech Corporation's portfolio covers an array of unparalleled filtration products designed to push the boundaries of: Execution of routine methods |
Research and development & fully commercialized |
USA |
Sterlitech is an industry leader focused on unique micro and sub-micron filtration products |
https://www.sterlitech.com/
|
Membrane development |
Application innovation |
Small-scale processing |
Aquaporin176 |
Aquaporins were discovered in 1983 by Peter Agre. The company uses aquaporins to purify water on a large scale |
Forward osmosis, zero liquid discharge, semiconductor wastewater treatment, leachate treatment, food industry processing, water reuse |
Commercialized |
Denmark |
Aquaporin is dedicated to becoming a leader in water purification through industrial biotechnological techniques |
https://aquaporin.com/
|
Aquafortus177 |
Aquafortus was founded in New Zealand to develop novel and proprietary zero liquid discharge technology |
Brine management, wastewater treatment, oil and gas, food and beverage, industrial effluent treatment |
Commercialized |
New Zealand |
Aquafortus develops and holds multiple patents on non-thermal, continuous and re-generable ZLD technology |
http://www.aquafortus.com/
|
FTSH20 ref. 178 |
Leading service provider of membrane-based water treatment technologies including forward osmosis (FO) and high brine concentration recovery (HBCR) |
FTSH2O™ FO membranes are ideal for applications where the feed stream contains high levels of suspended solids or high salinity |
Commercialized |
Albany, Oregon, New York, Boston, Seattle, Beijing, Shanghai |
FTS is a pioneer in the application of FO to treat difficult industrial, municipal, and agricultural waters and provide fresh water for reuse |
http://ftsh2o.com/
|
KOCH Membrane Systems (KMS)179 |
KMS was first established in 1963 as ABCOR Inc., a company built on separation and purification technology developed by scientists at the Massachusetts Institute of Technology |
Specialty in the manufacture of a range of membranes (UF, MF, RO, and NF) and systems for food, beverage and life sciences markets, automotive, municipal water/wastewater, textile, pulp and paper, pharmaceuticals, etc. |
Fully commercialized, research & development |
USA |
Koch Membrane Systems (KMS) has announced the launch of its TIDAL forward osmosis (FO) technology tailored to the food, beverage and life science sectors. The TIDAL FO technology enables product concentration without heat |
https://www.kochmembrane.com/en-US/about
|
Hyrec180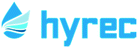 |
Founded in 2016. |
Textile, petrochemical & chemical, mining, oil & gas, power, desalination, wastewater treatment, mineral recovery, ZLD |
R&D, Pilot Plant |
Turkey, Bahrain |
Hyrec's mission is to create value by developing innovative, water treatment solutions.http://www.hyrec.co/industries/ |
Toyobo181 |
Founded in 1870. Original business: textiles |
Seawater desalination, pressure retarded osmosis, wastewater treatment, hollow fibre FO membranes, Industrial wastewater concentration |
Fully commercialized |
Japan |
Toyobo Co., Ltd. is one of Japan's top makers of fibers and textiles, including synthetic fibers and natural fibers, such as cotton and wool |
https://www.toyobo-global.com/
|
Ederna182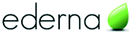 |
Founded in 2007 – TB Brown Group has acquired Ederna. As an instant coffee specialist, TB Brown will help Ederna accelerate the commercial development of its proprietary technology in coffee applications, food and beverage industries |
food & beverages, food processing, biotechnology |
Research & development, fully commercialized, pilot scale trials |
Netherlands |
Ederna has patented the next generation of cold concentration technology. This innovative process, called evapEOs®, allows new natural functional and food ingredients to be developed with high benefit and at reduced production costs. |
http://www.ederna.com/
|
Aromatec183 |
Aromatec Pte Ltd was established in 2018 |
Aromatec offers a range of membrane-based solutions for “cold” concentration. Concentration of flavours and fragrances, dairy production, fruit juice and vegetable production |
Commercialized |
Singapore |
Conventional concentration technologies include in particular evaporation or reverse osmosis (RO) membranes |
https://aromatec.biz/
|
Trevi Systems184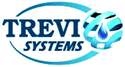 |
Founded in 2010 |
Renewables and the environment, groundwater treatment, specialty chemicals, wastewater treatment and pharmaceuticals treatment & desalination |
Research and development, pre commercialized |
USA |
Forward osmosis water purification systems for desalination of seawater, brackish water as well as produced water, and industrial and municipal wastewater |
https://www.trevisystems.com/
|
Darco Water Technologies185 |
Singapore-based investment holding company engaged in designing, building, operating and maintaining of water management processes that employ membrane, ion exchange and thermal technologies |
We specialize in designing, fabricating, assembling, installing and commissioning engineered water purification, wastewater, and vacuum installation systems |
Fully commercialized |
Singapore |
Extensive knowledge and expertise in building and operating FO systems |
http://www.darcowater.com/
|
|
Porifera186 |
Founded in 2009 |
Product concentration, water reuse, food and beverage, oil and gas and waste minimization |
Fully commercialized |
California, USA |
Providing forward osmosis solutions for low cost product concentration, waste reduction, and water reuse |
http://www.porifera.com/
|
Berghof Membrane Technology GmbH187 |
Over 50 years of experience in membrane filtration |
Membrane bioreactors (MBRs), food & beverage, chemical industry, brine polishing & recovery, oil & gas, dairy |
Fully commercialized |
The Netherlands |
Leading manufacturer of tubular membranes for the filtration and separation of process streams and wastewater in a variety of industries including dairy, landfills, mining, food & beverage, chemical & pharmaceutical, and oil & gas |
https://www.berghofmembranes.com/
|
TORAY188 |
Founded in 1926. Toray membrane offers integrated skills and expertise in water and wastewater treatment technologies, high quality membranes |
Chemicals, textiles, membranes, dairy, specialty, design, technical knowledge |
Fully commercialized, R&D |
USA, Switzerland, Spain, China, Singapore, Japan |
Toray Industries, Inc. is a multinational corporation headquartered in Japan that specializes in industrial products centered on technologies in organic synthetic chemistry, polymer chemistry, and biochemistry |
The niche applications of the FO process can be divided into two categories: a) application of FO with product water recovery and b) application of FO without product water recovery (i.e. osmotic concentration/dilution). Due to the various challenges with product water recovery, many FO applications are being classified as not cost effective. On the other hand, many of the FO applications that are shown to be promising & cost effective are based on the osmotic concentration/dilution concept. A part of this concept has been already discussed in section 3.2. The majority of the FO systems implemented in the market come with the application of FO with product water recovery. Recently, Koch Membrane Systems (KMS) has announced the launch of its TIDAL Forward Osmosis (FO) technology tailored to the food, beverage and life science sectors. The TIDAL FO technology enables product concentration without heat. This is another example of FO application without product water recovery. Aromatec Pte Ltd was established in 2018 and they offer a range of membrane-based solutions for “cold” concentration, such as concentration of flavours and fragrances, dairy production, and fruit juice and vegetable production. Thus Aromatec technology is also an interesting example for FO application with direct use of the concentrated FS. Bergh of Membrane Technology GmbH is another company which has demonstrated their visibility in the deployment of the FO process with and without product water recovery.
6. Life cycle cost analysis (LCCA) of the FO process
LCCA is a method to analyze the total cost as well as a wide range of cost elements of a system, including design, development and production costs, investment costs, operation and maintenance costs, and disposal costs throughout its life cycle, to determine the cost-effectiveness of the options among different configurations, systems, technologies, processes, services, feedstocks, and production alternatives.189 In other words, LCCA of a system is the total cost of acquiring and utilizing a system over its entire life span. LCCA includes all costs incurred from the point at which the decision is made to acquire a system, through operational life, to eventual disposal of the system.190 According to David and Lisnianski, the different steps for performing the LCCA process are depicted in Fig. 10.
 |
| Fig. 10 Different steps in the LCCA process. | |
Recently, several researchers have performed and reported the LCCA and techno-economic feasibility of the FO process and hybrid FO processes for different applications. Bryan et al.191 reported the economic assessment and LCCA of engineered osmosis and osmotic dilution processes for water treatment of Haynesville shale pit water. As per their investigations, FO is a more sustainable process for oil and gas (O&G) exploration wastewater treatment. Through their LCCA, they evaluated that FO, as an engineered osmosis and osmotic dilution (ODN) process, would reduce the economic and environmental impact for O&G exploration and associated pit water recovery. Low energy requirements of the FO process without any upstream pretreatment would significantly reduce the environmental impact. It was calculated that the pit water management cost could potentially be reduced by about 60% when the FO process was operated at 75% water recovery in comparison to cost requirements for deep well injection and pit water transportation cost, which can be reduced to 63%.
Hancock et al.192 carried out a comparative LCA methodology in order to distinguish between an innovative combined process consisting of conventional seawater reverse osmosis and FO–ODN mode and two more processes: (a) an independent SWRO system and (b) a hybrid SWRO and dual barrier water separation system with NF followed by RO. It was observed that the bottlenecks for the commercialization of the FO–SWRO process are optimized design of the FO membrane module and FO membrane fouling. System optimization analysis also revealed that the environmental impact of the combined FO–SWRO process compared to the SWRO process could be reduced by more than 25%, by tripling FO water flux (membrane efficiency), doubling membrane packing density and optimizing the FO process. The innovative combined NF–SWRO treatment of wastewater and seawater could also yield similar ranges of environmental impact.
In 2016, Linares et al.193 carried out an interesting study on the detailed economic analysis on capital expenses (CAPEX) and operational expenses (OPEX) for: i) a conventional SWRO process, ii) a hybrid process of FO–LPRO, and iii) a hybrid of MBR–RO–AOP (membrane bioreactor–reverse osmosis–advanced oxidation process) for wastewater treatment and reuse. In this study, the most governing parameters influencing the economic viability of a hybrid FO–LPRO system have been derived by means of a detailed sensitive analysis. They have considered a FO–LPRO system with a production capacity of 100
000 m3 d−1 potable water for the LCCA. The important components involved in the analysis are costs for the FO and RO modules, required energy, characteristics of the feed and product water, materials, chemical operation and maintenance. The analysis reveals that the CAPEX for the FO–LPRO system is 21% higher than that for the conventional SWRO system. At the same time, the OPEX for the FO–LPRO system is 56% lower than that for the SWRO system because of the less fouling issue and less energy requirement. They calculated a 16% reduction in the total cost for the FO–LPRO system for the production of potable water compared to the conventional SWRO system.
The CAPEX and OPEX of FO–LPRO systems in comparison to MBR–RO–AOP systems have been calculated to be 7% lower and 9% higher, respectively. Therefore, there is no prominent reduction in the unit water production for both systems. With the development of efficient FO membranes and modules with optimized packing density and water permeation flux, the cost for overall water production could be further lowered and this would be advantageous to hybrid FO–LPRO systems over conventional water treatment processes.
In 2017, Kim et al.194 carried out a study on the environmental and economic impacts of the fertilizer drawn forward osmosis (FDFO) and NF hybrid system and compared them with conventional SWRO hybrid systems using pre-treatment processes such as MF or UF. According to their findings, the FDFO–NF hybrid system using a TFC-FO membrane had less environmental impact than conventional RO hybrid systems due to lower consumption of energy and cleaning chemicals. The energy requirement for the treatment of mine impaired water by the FDFO–NF hybrid system was calculated to be 1.08 kW h m−3, which is 13.6% less than that of MF–RO and 21% less than that of UF–RO under similar initial feed solutions. The results of the above study clearly show that there is some positive potential of FDFO–NF for practical application with the development of a more efficient TFC-FO membrane and cost effective membrane module for the FO process. However, the improvement of efficient FO membranes towards the commercial scale is still open and thus detailed study of the fouling behavior and effective cleaning strategies is further needed for precise LCCA of the FO process.
In 2012, Mauter and Dzombak195 investigated the techno-economic feasibility of the FO process using ammonia–carbon dioxide as the DS (NH4HCO3 FO) – which is a two-step waste heat driven process in which the DS draws fresh water across the membrane by means of an osmotic pressure gradient. The second step is the regeneration of the draw solution by means of waste heat using a distillation column. In this work they have considered the waste heat generated at U.S. coal, nuclear, and natural gas plants and they have estimated the quantity, quality, and spatio-temporal availability. The potential of NH4HCO3 FO in order to treat flue gas desulfurization (FGD) wastewater, gasification wastewater, and boiler feed-water has been assessed. The costs of NH4HCO3 FO using waste heat for FGD and gasification wastewater treatment to ZLD and boiler feed-water treatment are $2.20–$2.40 per m3 and $0.35–$0.65 per m3, respectively. In comparison to mechanical vapor compression and crystallization for ZLD wastewater treatment and reverse osmosis for boiler feed-water treatment technologies, waste heat driven NH4HCO3 FO is cost competitive for ZLD wastewater treatment, but not for boiler feed-water treatment. They have estimated that the NH4HCO3 FO process would reduce the cost of ZLD by $0.30– $1.20 per m3.
Most recently, Hamid et al.196 reported the results of economic, energy and carbon footprint assessment of integrated FO–MBR for the treatment of urban wastewater using a FO membrane with 15 L m−2 h−1 flux, 80% water recovery and membrane cost of 50$/m2 – expensive in comparison to a microfiltration (MF) membrane. They considered three different scenarios as illustrated in Fig. 11: (A) FO–aerobic MBR (FOAeMBR); (B) an integrated RO–FOAeMBR system; (C) a hybrid of FO–anaerobic MBR (FOAnMBR) with a partial nitrification/anammox (PN/AMOX) process. In this study, the overall costs in scenarios A and B were higher with FO than MF by $0.16 per m3 and $0.75 per m3, respectively. There is no significant difference in the cost of wastewater treatment using scenario C ($1.1 per m3), compared to the MF process. In addition to that, the GHG emission in scenario C is as low as 0.93 kg CO2 equivalent per cubic meter and it was calculated to be 1.5 and 4.1 times lower than scenarios A and B, respectively. With the production of more efficient membranes with low cost and high flux, more optimized modules and processes could further reduce the overall cost and carbon footprint.
 |
| Fig. 11 Schematic illustrations of different scenarios for urban wastewater treatment.196 | |
7. Conclusion
There is a wide range of industrial applications where osmotically driven membrane processes may be applied. There are also relatively few commercial applications and only a few successful companies that have focused on utilizing forward osmosis technology, but this is currently expanding. There are a number of industrial applications that have great potential for FO to be used as both an independent and a hybrid system, in conjunction with other technologies available. They have been covered in this review and they include the oil and gas industry, wastewater, desalination and pharmaceutical industries, amongst others. Unfortunately, it is still challenging to directly compare the efficiency of various application bench scale experiments and pilot scale studies because of the discrepancies and differences in the set ups and the operational variables and conditions involved. The focus on more research in the area of FO will further increase the chances of establishing FO as a viable treatment technology in the future, and give rise to even more industrial applications. The limitations and challenges as well as the benefits of forward osmosis as a viable technology have also been highlighted within this paper. These have to be taken into account and addressed by researchers in the future to ensure that it can be applied to many applications.
Despite operating at lower pressure, fouling is one of the major challenges in FO membranes as it can significantly affect the permeate flux and quality. Physical and chemical cleaning methods as well as pretreatment units are commonly used to address fouling issues in membranes. Physical cleaning that includes cross-flow shearing and bubbly flow is capable of minimizing flux decline over long-term operation, while chemical cleaning is much more effective in controlling biofouling. Pretreatment using coagulation, oxidation and adsorption processes can also be effectively used to mitigate fouling. Recent fouling related studies have focused on the development of novel materials for membrane surface modifications to alleviate fouling issues.
An effective draw solute must be low-cost, capable of generating high osmotic pressure, of low reverse solute flux, non-toxic, and economic to regenerate. Small ionic salts are capable of generating high osmotic pressures, have lower concentration polarization and can be regenerated with established RO, but on the other hand have relatively higher reverse solute diffusion. Other innovative draw solutes have been explored, including polyelectrolytes, hydrogels, stimuli (thermo, pH)-responsive polymers and nanoparticles coated with hydrophilic groups. Though these polymers and nanoparticles of larger sizes have lower reverse salt diffusion and easy regeneration approaches, they could not compete with smaller molecules for the high osmotic pressures. Osmotic concentration or dilution is the process to leverage the salinity difference between two natural solutions (such as seawater and brine water) to drive water permeation flux through FO membranes. Osmotic concentration or dilution offers the potential for energy-efficient FO operation without the need for a draw solution regeneration process. Moreover, environmental benefits could be achieved by reducing the salinity of brine water, or reducing the volume of the impaired water, discharged to the aquatic ecosystem.
As a membrane-based water treatment technology, efficient FO membranes are one of the inevitable components in an FO process. As a matured membrane technology, the RO membrane in an RO process was the benchmark of FO membranes at the earlier stages of FO process development. However, researchers have since developed various types of cost effective, fouling resistant, highly water permeable membranes with the ability to retain solutes and reject contaminants. Hollow fiber membranes have the advantage of a large surface area to volume ratio and thereby improved packing density with small footprint compared to flat sheet membranes. Several start-up companies have been already introduced into the market in order to commercialize FO membranes. The latest trends in FO membrane fabrication are based on the incorporation of nanostructured materials, fouling resistant materials and biomimetic molecules in order to enhance the membrane efficiency and process performance. Still, it is clear that there are lots of areas to be improved in the fabrication of FO membranes in order to make the FO process more efficient and economically feasible. LCCA and techno-economic feasibility study are also very important aspects of any technology in order to move forward to the market. Most of the studies reveal that FO can be a competitive water treatment technology with the help of more efficient membranes, ideal draw solutions, optimal process designs and identification of niche applications.
Conflicts of interest
There are no conflicts to declare.
References
- D. L. Shaffer, J. R. Werber, H. Jaramillo, S. Lin and M. Elimelech, Forward osmosis: Where are we now?, Desalination, 2015, 356, 271–284 CrossRef CAS
.
- F. Zamani, J. W. Chew, E. Akhondi, W. B. Krantz and A. G. Fane, Unsteady-state shear strategies to enhance mass-transfer for the implementation of ultrapermeable membranes in reverse osmosis: A review, Desalination, 2015, 356, 328–348 CrossRef CAS
.
- T.-S. Chung, X. Li, R. C. Ong, Q. Ge, H. Wang and G. Han, Emerging forward osmosis (FO) technologies and challenges ahead for clean water and clean energy applications, Curr. Opin. Chem. Eng., 2012, 1, 246–257 CrossRef CAS
.
- S. Phuntsho, S. Sahebi, T. Majeed, F. Lotfi, J. E. Kim and H. K. Shon, Assessing the major factors affecting the performances of forward osmosis and its implications on the desalination process, Chem. Eng. J., 2013, 231, 484–496 CrossRef CAS
.
- N. Widjojo, T.-S. Chung, M. Weber, C. Maletzko and V. Warzelhan, A sulfonated polyphenylenesulfone (sPPSU) as the supporting substrate in thin film composite (TFC) membranes with enhanced performance for forward osmosis (FO), Chem. Eng. J., 2013, 220, 15–23 CrossRef CAS
.
- Y.-N. Wang, K. Goh, X. Li, L. Setiawan and R. Wang, Membranes and processes for forward osmosis-based desalination: Recent advances and future prospects, Desalination, 2018, 434, 81–99 CrossRef CAS
.
- L. Chekli, S. Phuntsho, J. E. Kim, J. Kim, J. Y. Choi, J.-S. Choi, S. Kim, J. H. Kim, S. Hong, J. Sohn and H. K. Shon, A comprehensive review of hybrid forward osmosis systems: Performance, applications and future prospects, J. Membr. Sci., 2016, 497, 430–449 CrossRef CAS
.
- A. J. Ansari, F. I. Hai, W. E. Price, J. E. Drewes and L. D. Nghiem, Forward osmosis as a platform for resource recovery from municipal wastewater - A critical assessment of the literature, J. Membr. Sci., 2017, 529, 195–206 CrossRef CAS
.
- R. Valladares Linares, Z. Li, S. Sarp, S. S. Bucs, G. Amy and J. S. Vrouwenvelder, Forward osmosis niches in seawater desalination and wastewater reuse, Water Res., 2014, 66, 122–139 CrossRef CAS PubMed
.
- I. Ibrar, A. Altaee, J. L. Zhou, O. Naji and D. Khanafer, Challenges and potentials of forward osmosis process in the treatment of wastewater, Crit. Rev. Environ. Sci. Technol., 2019, 1–45 Search PubMed
.
- W. Xu, Q. Chen and Q. Ge, Recent advances in forward osmosis (FO) membrane: Chemical modifications on membranes for FO processes, Desalination, 2017, 419, 101–116 CrossRef CAS
.
- B. Kim, G. Gwak and S. Hong, Review on methodology for determining forward osmosis (FO) membrane characteristics: Water permeability (A), solute permeability (B), and structural parameter (S), Desalination, 2017, 422, 5–16 CrossRef CAS
.
- N. Akther, A. Sodiq, A. Giwa, S. Daer, H. A. Arafat and S. W. Hasan, Recent advancements in forward osmosis desalination: A review, Chem. Eng. J., 2015, 281, 502–522 CrossRef CAS
.
- J. Herron, US7445712B2, 2008
.
- R. C. Ong and T.-S. Chung, Fabrication and positron annihilation spectroscopy (PAS) characterization of cellulose triacetate membranes for forward osmosis, J. Membr. Sci., 2012, 394–395, 230–240 CrossRef CAS
.
- R. Hausman, B. Digman, I. C. Escobar, M. Coleman and T.-S. Chung, Functionalization of polybenzimidizole membranes to impart negative charge and hydrophilicity, J. Membr. Sci., 2010, 363, 195–203 CrossRef CAS
.
- Q. Yang, K. Y. Wang and T.-S. Chung, Dual-Layer Hollow Fibers with Enhanced Flux As Novel Forward Osmosis Membranes for Water Production, Environ. Sci. Technol., 2009, 43, 2800–2805 CrossRef CAS PubMed
.
- K. Y. Wang, R. C. Ong and T.-S. Chung, Double-Skinned Forward Osmosis Membranes for Reducing Internal Concentration Polarization within the Porous Sublayer, Ind. Eng. Chem. Res., 2010, 49, 4824–4831 CrossRef CAS
.
- J. Su, Q. Yang, J. F. Teo and T.-S. Chung, Cellulose acetate nanofiltration hollow fiber membranes for forward osmosis processes, J. Membr. Sci., 2010, 355, 36–44 CrossRef CAS
.
- J. Su and T.-S. Chung, Sublayer structure and reflection coefficient and their effects on concentration polarization and membrane performance in FO processes, J. Membr. Sci., 2011, 376, 214–224 CrossRef CAS
.
- S. Zhang, K. Y. Wang, T.-S. Chung, Y. C. Jean and H. Chen, Molecular design of the cellulose ester-based forward osmosis membranes for desalination, Chem. Eng. Sci., 2011, 66, 2008–2018 CrossRef CAS
.
- Y. Yu, S. Seo, I.-C. Kim and S. Lee, Nanoporous polyethersulfone (PES) membrane with enhanced flux applied in forward osmosis process, J. Membr. Sci., 2011, 375, 63–68 CrossRef CAS
.
- M. F. Flanagan and I. C. Escobar, Novel charged and hydrophilized polybenzimidazole (PBI) membranes for forward osmosis, J. Membr. Sci., 2013, 434, 85–92 CrossRef CAS
.
- K. Y. Wang, T.-S. Chung and G. Amy, Developing thin-film-composite forward osmosis membranes on the PES/SPSf substrate through interfacial polymerization, AIChE J., 2012, 58, 770–781 CrossRef CAS
.
- X. Li, K. Y. Wang, B. Helmer and T.-S. Chung, Thin-Film Composite Membranes and Formation Mechanism of Thin-Film Layers on Hydrophilic Cellulose Acetate Propionate Substrates for Forward Osmosis Processes, Ind. Eng. Chem. Res., 2012, 51, 10039–10050 CrossRef CAS
.
- X. Song, Z. Liu and D. D. Sun, Nano Gives the Answer: Breaking the Bottleneck of Internal Concentration Polarization with a Nanofiber Composite Forward Osmosis Membrane for a High Water Production Rate, Adv. Mater., 2011, 23, 3256–3260 CrossRef CAS PubMed
.
- S. Shokrollahzadeh and S. Tajik, Fabrication of thin film composite forward osmosis membrane using electrospun polysulfone/polyacrylonitrile blend nanofibers as porous substrate, Desalination, 2018, 425, 68–76 CrossRef CAS
.
-
S. Loeb and S. Sourirajan, Sea water demineralization by means of an osmotic membrane, 1963, pp. 117–132 Search PubMed
.
-
J. E. Cadotte, US4277344A, 1979
.
- Q. Saren, C. Q. Qiu and C. Y. Tang, Synthesis and Characterization of Novel Forward Osmosis Membranes based on Layer-by-Layer Assembly, Environ. Sci. Technol., 2011, 45, 5201–5208 CrossRef CAS PubMed
.
- C. Qiu, S. Qi and C. Y. Tang, Synthesis of high flux forward osmosis membranes by chemically crosslinked layer-by-layer polyelectrolytes, J. Membr. Sci., 2011, 381, 74–80 CrossRef CAS
.
- H. Wang, T.-S. Chung, Y. W. Tong, K. Jeyaseelan, A. Armugam, Z. Chen, M. Hong and W. Meier, Highly Permeable and Selective Pore-Spanning Biomimetic Membrane Embedded with Aquaporin Z, Small, 2012, 8, 1185–1190 CrossRef CAS PubMed
.
- C. Y. Tang, Y. Zhao, R. Wang, C. Hélix-Nielsen and A. G. Fane, Desalination by biomimetic aquaporin membranes: Review of status and prospects, Desalination, 2013, 308, 34–40 CrossRef CAS
.
-
E. J. Breton, Water and Ion Flow through Imperfect Osmotic Membranes, 1957 Search PubMed
.
- J. O. Kessler and C. D. Moody, Drinking water from sea water by forward osmosis, Desalination, 1976, 18, 297–306 CrossRef CAS
.
-
G. W. Batchelder, US3171799A, 1965
.
-
HTI Water, Forward Osmosis Water Filtration Products, http://www.htiwater.com/, (accessed 1 February 2020) Search PubMed
.
- J. R. McCutcheon, R. L. McGinnis and M. Elimelech, A novel ammonia—carbon dioxide forward (direct) osmosis desalination process, Desalination, 2005, 174, 1–11 CrossRef CAS
.
- T. Y. Cath, M. Elimelech, J. R. McCutcheon, R. L. McGinnis, A. Achilli, D. Anastasio, A. R. Brady, A. E. Childress, I. V. Farr, N. T. Hancock, J. Lampi, L. D. Nghiem, M. Xie and N. Y. Yip, Standard Methodology for Evaluating Membrane Performance in Osmotically Driven Membrane Processes, Desalination, 2013, 312, 31–38 CrossRef CAS
.
-
X. Li, T. He, P. Dou and S. Zhao, in Comprehensive Membrane Science and Engineering, Elsevier, 2017, pp. 95–123 Search PubMed
.
- T. P. N. Nguyen, E.-T. Yun, I.-C. Kim and Y.-N. Kwon, Preparation of cellulose triacetate/cellulose acetate (CTA/CA)-based membranes for forward osmosis, J. Membr. Sci., 2013, 433, 49–59 CrossRef CAS
.
- J. Su, R. C. Ong, P. Wang, T.-S. Chung, B. J. Helmer and J. S. de Wit, Advanced FO membranes from newly synthesized CAP polymer for wastewater reclamation through an integrated FO-MD hybrid system, AIChE J., 2013, 59, 1245–1254 CrossRef CAS
.
- S. Zhang, K. Y. Wang, T.-S. Chung, H. Chen, Y. C. Jean and G. Amy, Well-constructed cellulose acetate membranes for forward osmosis: Minimized internal concentration polarization with an ultra-thin selective layer, J. Membr. Sci., 2010, 360, 522–535 CrossRef CAS
.
- J. Su, S. Zhang, H. Chen, H. Chen, Y. C. Jean and T.-S. Chung, Effects of annealing on the microstructure and performance of cellulose acetate membranes for pressure-retarded osmosis processes, J. Membr. Sci., 2010, 364, 344–353 CrossRef CAS
.
- N. Y. Yip, A. Tiraferri, W. A. Phillip, J. D. Schiffman and M. Elimelech, High Performance Thin-Film Composite Forward Osmosis Membrane, Environ. Sci. Technol., 2010, 44, 3812–3818 CrossRef CAS PubMed
.
- R. Wang, L. Shi, C. Y. Tang, S. Chou, C. Qiu and A. G. Fane, Characterization of novel forward osmosis hollow fiber membranes, J. Membr. Sci., 2010, 355, 158–167 CrossRef CAS
.
- N. Widjojo, T.-S. Chung, M. Weber, C. Maletzko and V. Warzelhan, The role of sulphonated polymer and macrovoid-free structure in the support layer for thin-film composite (TFC) forward osmosis (FO) membranes, J. Membr. Sci., 2011, 383, 214–223 CrossRef CAS
.
- G. Han, S. Zhang, X. Li, N. Widjojo and T.-S. Chung, Thin film composite forward osmosis membranes based on polydopamine modified polysulfone substrates with enhancements in both water flux and salt rejection, Chem. Eng. Sci., 2012, 80, 219–231 CrossRef CAS
.
- S. Chou, L. Shi, R. Wang, C. Y. Tang, C. Qiu and A. G. Fane, Characteristics and potential applications of a novel forward osmosis hollow fiber membrane, Desalination, 2010, 261, 365–372 CrossRef CAS
.
- P. Sukitpaneenit and T.-S. Chung, High Performance Thin-Film Composite Forward Osmosis Hollow Fiber Membranes with Macrovoid-Free and Highly Porous Structure for Sustainable Water Production, Environ. Sci. Technol., 2012, 46, 7358–7365 CrossRef CAS PubMed
.
- P. Zhong, X. Fu, T.-S. Chung, M. Weber and C. Maletzko, Development of Thin-Film Composite forward Osmosis Hollow Fiber Membranes Using Direct Sulfonated Polyphenylenesulfone (sPPSU) as Membrane Substrates, Environ. Sci. Technol., 2013, 47, 7430–7436 CrossRef CAS PubMed
.
- T. Majeed, S. Phuntsho, S. Sahebi, J. E. Kim, J. K. Yoon, K. Kim and H. K. Shon, Influence of the process parameters on hollow fiber-forward osmosis membrane performances, Desalin. Water Treat., 2015, 54, 817–828 CrossRef CAS
.
- M. Shibuya, M. Yasukawa, S. Mishima, Y. Tanaka, T. Takahashi and H. Matsuyama, A thin-film composite-hollow fiber forward osmosis membrane with a polyketone hollow fiber membrane as a support, Desalination, 2017, 402, 33–41 CrossRef CAS
.
- L. Luo, P. Wang, S. Zhang, G. Han and T.-S. Chung, Novel thin-film composite tri-bore hollow fiber membrane fabrication for forward osmosis, J. Membr. Sci., 2014, 461, 28–38 CrossRef CAS
.
- J. Ren and J. R. McCutcheon, Polyacrylonitrile supported thin film composite hollow fiber membranes for forward osmosis, Desalination, 2015, 372, 67–74 CrossRef CAS
.
- L. Setiawan, R. Wang, K. Li and A. G. Fane, Fabrication of novel poly(amide–imide) forward osmosis hollow fiber membranes with a positively charged nanofiltration-like selective layer, J. Membr. Sci., 2011, 369, 196–205 CrossRef CAS
.
- M. Shibuya, M. Yasukawa, S. Goda, H. Sakurai, T. Takahashi, M. Higa and H. Matsuyama, Experimental and theoretical study of a forward osmosis hollow fiber membrane module with a cross-wound configuration, J. Membr. Sci., 2016, 504, 10–19 CrossRef CAS
.
- M. Shibuya, M. Yasukawa, T. Takahashi, T. Miyoshi, M. Higa and H. Matsuyama, Effects of operating conditions and membrane structures on the performance of hollow fiber forward osmosis membranes in pressure assisted osmosis, Desalination, 2015, 365, 381–388 CrossRef CAS
.
- S. Lin, Mass transfer in forward osmosis with hollow fiber membranes, J. Membr. Sci., 2016, 514, 176–185 CrossRef CAS
.
- N.-N. Bui, M. L. Lind, E. M. V. Hoek and J. R. McCutcheon, Electrospun nanofiber supported thin film composite membranes for engineered osmosis, J. Membr. Sci., 2011, 385–386, 10–19 CrossRef CAS
.
-
Singapore International Water Week 2014-TOYOBO Co., Ltd., https://www.toyobo-global.com/news/pdf/2014/05/press20140521.pdf Search PubMed
.
- W. Zhao, H. Liu, Y. Liu, M. Jian, L. Gao, H. Wang and X. Zhang, Thin-Film Nanocomposite Forward-Osmosis Membranes on Hydrophilic Microfiltration Support with an Intermediate Layer of Graphene Oxide and Multiwall Carbon Nanotube, ACS Appl. Mater. Interfaces, 2018, 10, 34464–34474 CrossRef CAS PubMed
.
- D. Roy, M. Rahni, P. Pierre and V. Yargeau, Forward osmosis for the concentration and reuse of process saline wastewater, Chem. Eng. J., 2016, 287, 277–284 CrossRef CAS
.
- M. Zhan, G. Gwak, D. I. Kim, K. Park and S. Hong, Quantitative analysis of the irreversible membrane fouling of forward osmosis during wastewater reclamation: Correlation with the modified fouling index, J. Membr. Sci., 2020, 597, 117757 CrossRef
.
-
R. Valladares Linares and L. Francis, in Membrane-Based Salinity Gradient Processes for Water Treatment and Power Generation, ed. S. Sarp and N. Hilal, Elsevier, 2018, p. 362 Search PubMed
.
- J. Ren and J. R. McCutcheon, A new commercial biomimetic hollow fiber membrane for forward osmosis, Desalination, 2018, 442, 44–50 CrossRef CAS
.
- W. Xie, F. He, B. Wang, T.-S. Chung, K. Jeyaseelan, A. Armugam and Y. W. Tong, An aquaporin-based vesicle-embedded polymeric membrane for low energy water filtration, J. Mater. Chem. A, 2013, 1, 7592 RSC
.
- Y. Wang, Z. Fang, S. Zhao, D. Ng, J. Zhang and Z. Xie, Dopamine incorporating forward osmosis membranes with enhanced selectivity and antifouling properties, RSC Adv., 2018, 8, 22469–22481 RSC
.
- Y. Li, Y. Yang, C. Li and L. Hou, Comparison of performance and biofouling resistance of thin-film composite forward osmosis membranes with substrate/active layer modified by graphene oxide, RSC Adv., 2019, 9, 6502–6509 RSC
.
- D. Qin, Z. Liu, H. Bai and D. D. Sun, Three-dimensional architecture constructed from a graphene oxide nanosheet–polymer composite for high-flux forward osmosis membranes, J. Mater. Chem. A, 2017, 5, 12183–12192 RSC
.
- A. Achilli, T. Y. Cath and A. E. Childress, Selection of inorganic-based draw solutions for forward osmosis applications, J. Membr. Sci., 2010, 364, 233–241 CrossRef CAS
.
- C. H. Tan and H. Y. Ng, A novel hybrid forward osmosis - nanofiltration (FO-NF) process for seawater desalination: Draw solution selection and system configuration, Desalin. Water Treat., 2010, 13, 356–361 CrossRef CAS
.
- Q. Ge, J. Su, G. L. Amy and T.-S. Chung, Exploration of polyelectrolytes as draw solutes in forward osmosis processes, Water Res., 2012, 46, 1318–1326 CrossRef CAS PubMed
.
- R. L. McGinnis, N. T. Hancock, M. S. Nowosielski-Slepowron and G. D. McGurgan, Pilot demonstration of the NH3/CO2 forward osmosis desalination process on high salinity brines, Desalination, 2013, 312, 67–74 CrossRef CAS
.
-
D. J. Briggs, United States Application, US20200023316, 2020 Search PubMed
.
- M. L. Stone, C. Rae, F. F. Stewart and A. D. Wilson, Switchable polarity solvents as draw solutes for forward osmosis, Desalination, 2013, 312, 124–129 CrossRef CAS
.
- Q. Ge, P. Wang, C. Wan and T.-S. Chung, Polyelectrolyte-Promoted Forward Osmosis–Membrane Distillation (FO–MD) Hybrid Process for Dye Wastewater Treatment, Environ. Sci. Technol., 2012, 46, 6236–6243 CrossRef CAS PubMed
.
-
B. S. Frank, US3670897A, 1970
.
- Z. Liu, H. Bai, J. Lee and D. D. Sun, A low-energy forward osmosis process to produce drinking water, Energy Environ. Sci., 2011, 4, 2582 RSC
.
- Q. Ge, J. Su, T.-S. Chung and G. Amy, Hydrophilic Superparamagnetic Nanoparticles: Synthesis, Characterization, and Performance in Forward Osmosis Processes, Ind. Eng. Chem. Res., 2011, 50, 382–388 CrossRef CAS
.
- Y. Cai, W. Shen, S. L. Loo, W. B. Krantz, R. Wang, A. G. Fane and X. Hu, Towards temperature driven forward osmosis desalination using Semi-IPN hydrogels as reversible draw agents, Water Res., 2013, 47, 3773–3781 CrossRef CAS PubMed
.
- C. Ju, C. Park, T. Kim, S. Kang and H. Kang, Thermo-responsive draw solute for forward osmosis process; Poly(ionic liquid) having lower critical solution temperature characteristics, RSC Adv., 2019, 9, 29493–29501 RSC
.
- T. Cath, A. Childress and M. Elimelech, Forward osmosis: Principles, applications, and recent developments, J. Membr. Sci., 2006, 281, 70–87 CrossRef CAS
.
- S. Phuntsho, H. K. Shon, S. Hong, S. Lee and S. Vigneswaran, A novel low energy fertilizer driven forward osmosis desalination for direct fertigation: Evaluating the performance of fertilizer draw solutions, J. Membr. Sci., 2011, 375, 172–181 CrossRef CAS
.
- J. Minier-Matar, A. Hussain, A. Janson, R. Wang, A. G. Fane and S. Adham, Application of forward osmosis for reducing volume of produced/Process water from oil and gas operations, Desalination, 2015, 376, 1–8 CrossRef CAS
.
- C. Kim, S. Lee, H. K. Shon, M. Elimelech and S. Hong, Boron transport in forward osmosis: Measurements, mechanisms, and comparison with reverse osmosis, J. Membr. Sci., 2012, 419–420, 42–48 CrossRef CAS
.
- T. Husnain, Y. Liu, R. Riffat and B. Mi, Integration of forward osmosis and membrane distillation for sustainable wastewater reuse, Sep. Purif. Technol., 2015, 156, 424–431 CrossRef CAS
.
- M. Xie, L. D. Nghiem, W. E. Price and M. Elimelech, A Forward Osmosis–Membrane Distillation Hybrid Process for Direct Sewer Mining: System Performance and Limitations, Environ. Sci. Technol., 2013, 47, 13486–13493 CrossRef CAS PubMed
.
- T. Cath, A. Childress and M. Elimelech, Forward osmosis: Principles, applications, and recent developments, J. Membr. Sci., 2006, 281, 70–87 CrossRef CAS
.
- J. Duan, E. Litwiller, S.-H. Choi and I. Pinnau, Evaluation of sodium lignin sulfonate as draw solute in forward osmosis for desert restoration, J. Membr. Sci., 2014, 453, 463–470 CrossRef CAS
.
- S. Adham, A. Hussain, J. Minier-Matar, A. Janson and R. Sharma, Membrane applications and opportunities for water management in the oil & gas industry, Desalination, 2018, 440, 2–17 CrossRef CAS
.
- A. Bogler, S. Lin and E. Bar-Zeev, Biofouling
of membrane distillation, forward osmosis and pressure retarded osmosis: Principles, impacts and future directions, J. Membr. Sci., 2017, 542, 378–398 CrossRef CAS
.
-
S. J. Khan, N. P. Hankins and L. C. Shen, in Emerging Membrane Technology for Sustainable Water Treatment, Elsevier Inc., 2016, pp. 277–296 Search PubMed
.
- Y. Chun, D. Mulcahy, L. Zou and I. S. Kim, A short review of membrane fouling in forward osmosis processes, Membranes, 2017, 7, 1–23 CrossRef
.
-
H. Li and V. Chen, in Membrane Technology, Elsevier Ltd, 2010, pp. 213–254 Search PubMed
.
- Y. Sun, J. Tian, Z. Zhao, W. Shi, D. Liu and F. Cui, Membrane fouling of forward osmosis (FO) membrane for municipal wastewater treatment: A comparison between direct FO and OMBR, Water Res., 2016, 104, 330–339 CrossRef CAS PubMed
.
- Q. Liu, G. Qiu, Z. Zhou, J. Li, G. L. Amy, J. Xie and J. Y. Lee, An Effective Design of Electrically Conducting Thin-Film Composite (TFC) Membranes for Bio and Organic Fouling Control in Forward Osmosis (FO), Environ. Sci. Technol., 2016, 50, 10596–10605 CrossRef CAS PubMed
.
- Y. Yu, S. Lee and S. K. Maeng, Forward osmosis membrane fouling and cleaning for wastewater reuse, J. Water Reuse Desalin., 2017, 7, 111–120 CrossRef
.
- B. Mi and M. Elimelech, Organic fouling of forward osmosis membranes: Fouling reversibility and cleaning without chemical reagents, J. Membr. Sci., 2010, 348, 337–345 CrossRef CAS
.
- E. Arkhangelsky, F. Wicaksana, C. Tang, A. A. Al-Rabiah, S. M. Al-Zahrani and R. Wang, Combined organic-inorganic fouling of forward osmosis hollow fiber membranes, Water Res., 2012, 46, 6329–6338 CrossRef CAS PubMed
.
- F. Lotfi, L. Chekli, S. Phuntsho, S. Hong, J. Y. Choi and H. K. Shon, Understanding the possible underlying mechanisms for low fouling tendency of the forward osmosis and pressure assisted osmosis processes, Desalination, 2017, 421, 89–98 CrossRef CAS
.
- S. Lee, H. K. Shon and S. Hong, Dewatering of activated sludge by forward osmosis (FO) with ultrasound for fouling control, Desalination, 2017, 421, 79–88 CrossRef CAS
.
- J. Lee, S. Kook, C. Lee and I. S. Kim, Effect of intermittent pressure-assisted forward osmosis (I-PAFO) on organic fouling, Desalination, 2017, 419, 60–69 CrossRef CAS
.
- X. Du, Y. Wang, F. Qu, K. Li, X. Liu, Z. Wang, G. Li and H. Liang, Impact of bubbly flow in feed channel of forward osmosis for wastewater treatment: Flux performance and biofouling, Chem. Eng. J., 2017, 316, 1047–1058 CrossRef CAS
.
- R. Valladares Linares, S. S. Bucs, Z. Li, M. AbuGhdeeb, G. Amy and J. S. Vrouwenvelder, Impact of spacer thickness on biofouling in forward osmosis, Water Res., 2014, 57, 223–233 CrossRef CAS PubMed
.
- Y. Sun, S. Gao, J. Tian, X. Hao, Z. Liu, W. Shi and F. Cui, Air bubbling for membrane fouling control in a submerged direct forward osmosis system for municipal wastewater treatment, Environ. Sci.: Water Res. Technol., 2019, 5, 684–692 RSC
.
- B. K. Pramanik, F. I. Hai and F. A. Roddick, Ultraviolet/persulfate pre-treatment for organic fouling mitigation of forward osmosis membrane: Possible application in nutrient mining from dairy wastewater, Sep. Purif. Technol., 2019, 217, 215–220 CrossRef CAS
.
- B. K. Pramanik, L. Shu, V. Jegatheesan and M. A. Bhuiyan, Effect of the coagulation/persulfate pre-treatment to mitigate organic fouling in the forward osmosis of municipal wastewater treatment, J. Environ. Manage., 2019, 249, 109394 CrossRef CAS PubMed
.
- B. Al Hawli, A. Benamor and A. A. Hawari, A hybrid electro-coagulation/forward osmosis system for treatment of produced water, Chem. Eng. Process., 2019, 143, 107621 CrossRef CAS
.
- B. Aftab, Y. S. Ok, J. Cho and J. Hur, Targeted removal of organic foulants in landfill leachate in forward osmosis system integrated with biochar/activated carbon treatment, Water Res., 2019, 160, 217–227 CrossRef CAS PubMed
.
- H. Yoon, Y. Baek, J. Yu and J. Yoon, Biofouling occurrence process and its control in the forward osmosis, Desalination, 2013, 325, 30–36 CrossRef CAS
.
- Y. Gao, Z. Fang, P. Liang and X. Huang, Direct concentration of municipal sewage by forward osmosis and membrane fouling behavior, Bioresour. Technol., 2018, 247, 730–735 CrossRef CAS PubMed
.
- R. Valladares Linares, Z. Li, V. Yangali-Quintanilla, Q. Li and G. Amy, Cleaning protocol for a FO membrane fouled in wastewater reuse, Desalin. Water Treat., 2013, 51, 4821–4824 CrossRef CAS
.
- X. Wang, T. Hu, Z. Wang, X. Li and Y. Ren, Permeability recovery of fouled forward osmosis membranes by chemical cleaning during a long-term operation of anaerobic osmotic membrane bioreactors treating low-strength wastewater, Water Res., 2017, 123, 505–512 CrossRef CAS PubMed
.
- X. Xu, H. Zhang, M. Yu, Y. Wang, T. Gao and F. Yang, Conductive thin film nanocomposite forward osmosis membrane (TFN-FO) blended with carbon nanoparticles for membrane fouling control, Sci. Total Environ., 2019, 697, 134050 CrossRef CAS PubMed
.
- X. Fan, Y. Liu, X. Quan and S. Chen, Highly Permeable Thin-Film Composite Forward Osmosis Membrane Based on Carbon Nanotube Hollow Fiber Scaffold with Electrically Enhanced Fouling Resistance, Environ. Sci. Technol., 2018, 52, 1444–1452 CrossRef CAS PubMed
.
- M. Qiu and C. He, Novel zwitterion-silver nanocomposite modified thin-film composite forward osmosis membrane with simultaneous improved water flux and biofouling resistance property, Appl. Surf. Sci., 2018, 455, 492–501 CrossRef CAS
.
- A. F. Faria, C. Liu, M. Xie, F. Perreault, L. D. Nghiem, J. Ma and M. Elimelech, Thin-film composite forward osmosis membranes functionalized with graphene oxide–silver nanocomposites for biofouling control, J. Membr. Sci., 2017, 525, 146–156 CrossRef CAS
.
- Y. Kang, S. Zheng, C. Finnerty, M. J. Lee and B. Mi, Regenerable Polyelectrolyte Membrane for Ultimate Fouling Control in Forward Osmosis, Environ. Sci. Technol., 2017, 51, 3242–3249 CrossRef CAS PubMed
.
- S. Adham, A. Hussain, J. Minier Matar, A. Janson and S. Gharfeh, Screening of advanced produced water treatment technologies: overview and testing results, IDA J. Desalin. Water Reuse, 2013, 5, 75–82 CrossRef CAS
.
- A. Haupt and A. Lerch, Forward Osmosis Application in Manufacturing Industries: A Short Review, Membranes, 2018, 8, 47 CrossRef PubMed
.
- Muhammad Yaqub and W. Lee, Zero-liquid discharge (ZLD) technology for resource recovery from wastewater: A review, Sci. Total Environ., 2019, 681, 551–563 CrossRef PubMed
.
- T. Tong and M. Elimelech, The Global Rise of Zero Liquid Discharge for Wastewater Management: Drivers, Technologies, and Future Directions, Environ. Sci. Technol., 2016, 50, 6846–6855 CrossRef CAS PubMed
.
- L. Chen, Y. Gu, C. Cao, J. Zhang, J.-W. Ng and C. Tang, Performance of a submerged anaerobic membrane bioreactor with forward osmosis membrane for low-strength wastewater treatment, Water Res., 2014, 50, 114–123 CrossRef CAS PubMed
.
- S.-F. Pan, Y. Dong, Y.-M. Zheng, L.-B. Zhong and Z.-H. Yuan, Self-sustained hydrophilic nanofiber thin film composite forward osmosis membranes: Preparation, characterization and application for simulated antibiotic wastewater treatment, J. Membr. Sci., 2017, 523, 205–215 CrossRef CAS
.
- N. Peng, N. Widjojo, P. Sukitpaneenit, M. M. Teoh, G. G. Lipscomb, T.-S. Chung and J.-Y. Lai, Evolution of polymeric hollow fibers as sustainable technologies: Past, present, and future, Prog. Polym. Sci., 2012, 37, 1401–1424 CrossRef CAS
.
- R. V. Linares, Z. Li, M. Elimelech, G. Amy and H. Vrouwenvelder, Recent Developments in Forward Osmosis Processes, Water Intell. Online, 2017, 16, 9781780408125 CrossRef
.
- L. A. Hoover, W. A. Phillip, A. Tiraferri, N. Y. Yip and M. Elimelech, Forward with Osmosis: Emerging Applications for Greater Sustainability, Environ. Sci. Technol., 2011, 45, 9824–9830 CrossRef CAS PubMed
.
- S. Phuntsho, S. Vigneswaran, J. Kandasamy, S. Hong, S. Lee and H. K. Shon, Influence of temperature and temperature difference in the performance of forward osmosis desalination process, J. Membr. Sci., 2012, 415–416, 734–744 CrossRef CAS
.
- J. L. Cartinella, T. Y. Cath, M. T. Flynn, G. C. Miller, K. W. Hunter and A. E. Childress, Removal of Natural Steroid Hormones from Wastewater Using Membrane Contactor Processes, Environ. Sci. Technol., 2006, 40, 7381–7386 CrossRef CAS PubMed
.
- Y. Kim, S. Li, L. Francis, Z. Li, R. V. Linares, A. S. Alsaadi, M. Abu-Ghdaib, H. S. Son, G. Amy and N. Ghaffour, Osmotically and Thermally Isolated Forward Osmosis-Membrane Distillation (FO-MD) Integrated Module, Environ. Sci. Technol., 2019, 53, 3488–3498 CrossRef CAS PubMed
.
-
S. Zhang and A. G. Fane, in 13 AIChE Annual Meeting, 2013 Search PubMed.
- T. Y. Cath, N. T. Hancock, C. D. Lundin, C. Hoppe-Jones and J. E. Drewes, A multi-barrier osmotic dilution process for simultaneous desalination and purification of impaired water, J. Membr. Sci., 2010, 362, 417–426 CrossRef CAS
.
- V. Yangali-Quintanilla, Z. Li, R. Valladares, Q. Li and G. Amy, Indirect desalination of Red Sea water with forward osmosis and low pressure reverse osmosis for water reuse, Desalination, 2011, 280, 160–166 CrossRef CAS
.
-
K. Lampi, in The 3rd Osmosis Membrane Summit, 2012 Search PubMed.
- K. L. Hickenbottom, N. T. Hancock, N. R. Hutchings, E. W. Appleton, E. G. Beaudry, P. Xu and T. Y. Cath, Forward osmosis treatment of drilling mud and fracturing wastewater from oil and gas operations, Desalination, 2013, 312, 60–66 CrossRef CAS
.
- S. Zhang, P. Wang, X. Fu and T.-S. Chung, Sustainable water recovery from oily wastewater via forward osmosis-membrane distillation (FO-MD), Water Res., 2014, 52, 112–121 CrossRef CAS PubMed
.
- D. L. Shaffer, L. H. Arias Chavez, M. Ben-Sasson, S. Romero-Vargas Castrillón, N. Y. Yip and M. Elimelech, Desalination and Reuse of High-Salinity Shale Gas Produced Water: Drivers, Technologies, and Future Directions, Environ. Sci. Technol., 2013, 47, 9569–9583 CrossRef CAS PubMed
.
- T. Liden, Z. L. Hildenbrand and K. A. Schug, Pretreatment Techniques for Produced Water with Subsequent Forward Osmosis Remediation, Water, 2019, 11, 1437 CrossRef CAS
.
-
P. Nicoll, N. Thompson, V. Gray and Modern WaterPLC, in Cooling Technology Institute Annual Conference, 2012 Search PubMed.
- J. E. Kim, S. Phuntsho and H. K. Shon, Pilot-scale nanofiltration system as post-treatment for fertilizer-drawn forward osmosis desalination for direct fertigation, Desalin. Water Treat., 2013, 51, 6265–6273 CrossRef CAS
.
- F. Carvalho, A. R. Prazeres and J. Rivas, Cheese whey wastewater: Characterization and treatment, Sci. Total Environ., 2013, 445–446, 385–396 CrossRef CAS PubMed
.
- H. Song, F. Xie, W. Chen and J. Liu, FO/MD hybrid system for real dairy wastewater recycling, Environ. Technol., 2018, 39, 2411–2421 CrossRef CAS PubMed
.
-
H. Ihalainen, M. Eng, Lappeenranta University of Technology, 2016 Search PubMed
.
- T. Ruprakobkit, L. Ruprakobkit and C. Ratanatamskul, Carboxylic acid concentration by forward osmosis processes: Dynamic modeling, experimental validation and simulation, Chem. Eng. J., 2016, 306, 538–549 CrossRef CAS
.
-
Technology For Humanitarian Action (International Humanitarian Affairs), ed. K. M. Cahill, Fordham University Press, 2004 Search PubMed
.
-
Hydration Technology Innovations LLC, Personal Desalination and Water Filters, http://www.htiwater.com/divisions/personal_hydration/index.html Search PubMed
.
- A. Y. Gebreyohannes, E. Curcio, T. Poerio, R. Mazzei, G. Di Profio, E. Drioli and L. Giorno, Treatment of Olive Mill Wastewater by Forward Osmosis, Sep. Purif. Technol., 2015, 147, 292–302 CrossRef CAS
.
- A. Thombre, J. Cardinal, A. DeNoto, S. Herbig and K. Smith, Asymmetric membrane capsules for osmotic drug delivery, J. Controlled Release, 1999, 57, 55–64 CrossRef CAS PubMed
.
- A. G. Thombre, J. R. Cardinal, A. R. DeNoto and D. C. Gibbes, Asymmetric membrane capsules for osmotic drug delivery II. In vitro and in vivo drug release performance, J. Controlled Release, 1999, 57, 65–73 CrossRef CAS PubMed
.
- Y. Lin and H. Ho, Investigations on the drug releasing mechanism from an asymmetric membrane-coated capsule with an in situ formed delivery orifice, J. Controlled Release, 2003, 89, 57–69 CrossRef CAS PubMed
.
- C. A. Nayak and N. K. Rastogi, Forward osmosis for the concentration of anthocyanin from Garcinia indica Choisy, Sep. Purif. Technol., 2010, 71, 144–151 CrossRef CAS
.
- K. Y. Wang, M. M. Teoh, A. Nugroho and T.-S. Chung, Integrated forward osmosis–membrane distillation (FO–MD) hybrid system for the concentration of protein solutions, Chem. Eng. Sci., 2011, 66, 2421–2430 CrossRef CAS
.
- K. M. Talaat, Dialysis fluid regeneration by forward osmosis: A feasible option for ambulatory dialysis systems, Saudi J. Kidney Dis. Transpl., 2010, 21(4), 748–749 Search PubMed
.
- G. Gwak, D. I. Kim and S. Hong, New industrial application of forward osmosis (FO): Precious metal recovery from printed circuit board (PCB) plant wastewater, J. Membr. Sci., 2018, 552, 234–242 CrossRef CAS
.
- L. Li, W. Shi and S. Yu, Research on Forward Osmosis Membrane Technology Still Needs Improvement in Water Recovery and Wastewater Treatment, Water, 2019, 12, 107 CrossRef
.
-
Integrating forward osmosis in thermal desalination processes, https://www.forwardosmosistech.com/integrating-forward-osmosis-in-thermal-desalination-processes/, (accessed 19 May 2020) Search PubMed
.
- M. Qasim, N. A. Darwish, S. Sarp and N. Hilal, Water desalination by forward (direct) osmosis phenomenon: A comprehensive review, Desalination, 2015, 374, 47–69 CrossRef CAS
.
- R. Kumar, S. Al-Haddad, M. Al-Rughaib and M. Salman, Evaluation of hydrolyzed poly(isobutylene-alt-maleic anhydride) as a polyelectrolyte draw solution for forward osmosis desalination, Desalination, 2016, 394, 148–154 CrossRef CAS
.
- I. Ibrar, O. Naji, A. Sharif, A. Malekizadeh, A. Alhawari, A. A. Alanezi and A. Altaee, A Review of Fouling Mechanisms, Control Strategies and Real-Time Fouling Monitoring Techniques in Forward Osmosis, Water, 2019, 11, 695 CrossRef CAS
.
- G. Chen, R. Liu, H. K. Shon, Y. Wang, J. Song, X.-M. Li and T. He, Open porous hydrophilic supported thin-film composite forward osmosis membrane via co-casting for treatment of high-salinity wastewater, Desalination, 2017, 405, 76–84 CrossRef CAS
.
- M. Ghanbari, D. Emadzadeh, W. J. Lau, H. Riazi, D. Almasi and A. F. Ismail, Minimizing structural parameter of thin film composite forward osmosis membranes using polysulfone/halloysite nanotubes as membrane substrates, Desalination, 2016, 377, 152–162 CrossRef CAS
.
- J. Lee, S. Kook, C. Lee and I. S. Kim, Effect of intermittent pressure-assisted forward osmosis (I-PAFO) on organic fouling, Desalination, 2017, 419, 60–69 CrossRef CAS
.
- Y.-N. Wang, R. Wang, W. Li and C. Y. Tang, Whey recovery using forward osmosis – Evaluating the factors limiting the flux performance, J. Membr. Sci., 2017, 533, 179–189 CrossRef CAS
.
-
W. Suwaileh, N. Pathak, H. Shon and N. Hilal, Forward osmosis membranes and processes: A comprehensive review of research trends and future outlook, 2020, vol. 485 Search PubMed
.
- P. S. Goh, A. F. Ismail, B. C. Ng and M. S. Abdullah, Recent Progresses of Forward Osmosis Membranes Formulation and Design for Wastewater Treatment, Water, 2019, 11, 2043 CrossRef CAS
.
- M. Mohammadifakhr, J. de Grooth, H. D. W. Roesink and A. J. B. Kemperman, Forward Osmosis: A Critical Review, Processes, 2020, 8, 404 CrossRef
.
- S. Sahebi, S. Phuntsho, J. Eun Kim, S. Hong and H. Kyong Shon, Pressure assisted fertiliser drawn osmosis process to enhance final dilution of the fertiliser draw solution beyond osmotic equilibrium, J. Membr. Sci., 2015, 481, 63–72 CrossRef CAS
.
- V. Sant'Anna, L. D. F. Marczak and I. C. Tessaro, Membrane concentration of liquid foods by forward osmosis: Process and quality view, J. Food Eng., 2012, 111, 483–489 CrossRef
.
- A. Barros, F. M. Nunes, B. Gonçalves, R. N. Bennett and A. P. Silva, Effect of cooking on total vitamin C contents and antioxidant activity of sweet chestnuts (Castanea sativa Mill.), Food Chem., 2011, 128, 165–172 CrossRef CAS PubMed
.
- V. Sanahuja-Embuena, G. Khensir, M. Yusuf, M. F. Andersen, X. T. Nguyen, K. Trzaskus, M. Pinelo and C. Helix-Nielsen, Role of Operating Conditions in a Pilot Scale Investigation of Hollow Fiber Forward Osmosis Membrane Modules, Membranes, 2019, 9, 66 CrossRef CAS PubMed
.
-
J. A. Korak and M. Arias-Paic, Forward Osmosis Evaluation and Applications for Reclamation, 2015 Search PubMed.
- Forward osmosis has attracted a lot of recent attention over the past few years but with limited market success. With several new companies entering the market and some early commercial installations, has the technology turned a corner? Jul 1st, 2017 Cont, https://www.waterworld.com/international/desalination/article/16201130/forward-osmosis-is-it-beginning-to-live-up-to-the-hype
.
-
Forward Water Technologies, https://forwardwater.com/technology-market/ Search PubMed
.
-
Laboratory Filtration Solutions and Equipment | Sterlitech, https://www.sterlitech.com/, (accessed 21 May 2020) Search PubMed
.
-
Hollow Fiber Forward Osmosis Modules - Aquaporin, https://aquaporin.com/forward-osmosis-membranes/, (accessed 12 February 2020) Search PubMed
.
-
Aquafortus ABX, http://www.aquafortus.com/technology, (accessed 12 February 2020) Search PubMed
.
-
FTSH20, http://ftsh2o.com/technologies/forward-osmosis/ Search PubMed
.
-
About, Koch Membrane Systems, https://www.kochmembrane.com/en-US/about, (accessed 21 May 2020) Search PubMed
.
-
Hyrec, http://www.hyrec.co/news-2/ Search PubMed
.
-
TOYOBO, https://www.toyobo-global.com/, (accessed 21 May 2020) Search PubMed
.
-
ederna, http://www.ederna.com/, (accessed 21 May 2020) Search PubMed
.
-
Aromatec, https://aromatec.biz/, (accessed 21 May 2020) Search PubMed
.
-
Desalination, Trevi Systems Inc, United States, https://www.trevisystems.com/, (accessed 12 February 2020) Search PubMed
.
-
Darco Water Technologies Limited, http://www.darcowater.com/, (accessed 21 May 2020) Search PubMed
.
-
Porifera, http://www.porifera.com/, (accessed 21 May 2020) Search PubMed
.
-
Berghof Membranes, The leader in UF tubular membrane filtration, https://www.berghofmembranes.com/, (accessed 21 May 2020) Search PubMed
.
-
Toray Membrane, TORAY, https://www.toraywater.com/, (accessed 21 May 2020) Search PubMed
.
-
Ş. Y. Balaman, in Decision-Making for Biomass-Based Production Chains, Elsevier, 2019, pp. 77–112 Search PubMed
.
- D. Elmakis and A. Lisnianski, Life cycle cost analysis: Actual problem in industrial management, J. Bus. Econ. Manag., 2006, 7, 5–8 CrossRef
.
- B. D. Coday, L. Miller-Robbie, E. G. Beaudry, J. Munakata-Marr and T. Y. Cath, Life cycle and economic assessments of engineered osmosis and osmotic dilution for desalination of Haynesville shale pit water, Desalination, 2015, 369, 188–200 CrossRef CAS
.
- N. T. Hancock, N. D. Black and T. Y. Cath, A comparative life cycle assessment of hybrid osmotic dilution desalination and established seawater desalination and wastewater reclamation processes, Water Res., 2012, 46, 1145–1154 CrossRef CAS PubMed
.
- R. Valladares Linares, Z. Li, V. Yangali-Quintanilla, N. Ghaffour, G. Amy, T. Leiknes and J. S. Vrouwenvelder, Life cycle cost of a hybrid forward osmosis – low pressure reverse osmosis system for seawater desalination and wastewater recovery, Water Res., 2016, 88, 225–234 CrossRef CAS PubMed
.
- J. E. Kim, S. Phuntsho, L. Chekli, S. Hong, N. Ghaffour, T. Leiknes, J. Y. Choi and H. K. Shon, Environmental and economic impacts of fertilizer drawn forward osmosis and nanofiltration hybrid system, Desalination, 2017, 416, 76–85 CrossRef CAS
.
-
M. Mauter and D. Dzombak, Evaluating the Techno-Economic Feasibility of Forward Osmosis Process Utilizing Low Grade Heat: Applications in Power Plant Water, Wastewater, and Reclaimed Water Treatment, 2017 Search PubMed.
- N. H. Ab Hamid, S. Smart, D. K. Wang, K. W. J. Koh, K. J. C. Ng and L. Ye, Economic, energy and carbon footprint assessment of integrated forward osmosis membrane bioreactor (FOMBR) process in urban wastewater treatment, Environ. Sci.: Water Res. Technol., 2020, 6, 153–165 RSC
.
|
This journal is © The Royal Society of Chemistry 2020 |
Click here to see how this site uses Cookies. View our privacy policy here.